Revolutionizing Precision: The Impact of Industry 4.0 on the Netherlands CNC Drilling Machine Market
views
Introduction
The Netherlands CNC Drilling Machine Market is experiencing a significant transformation as the Fourth Industrial Revolution, or Industry 4.0, continues to reshape manufacturing industries across the globe. As automation, Internet of Things (IoT) technology, and Artificial Intelligence (AI) are making their mark on the precision manufacturing sector, CNC (Computer Numerical Control) drilling machines in the Netherlands are benefiting from improved efficiency, precision, and versatility. The integration of these technologies is ushering in a new era of productivity, lowering operational costs, and enhancing the capabilities of drilling machines to meet the rising demands of various industries, including automotive, aerospace, and electronics.
In this article, we will explore the impact of Industry 4.0 on CNC drilling machines in the Netherlands and how automation, IoT, and AI are transforming the sector. We will also delve into the benefits, challenges, and future prospects of these advancements for businesses and manufacturers in the region.
The Role of Industry 4.0 in the Netherlands CNC Drilling Machine Market
Industry 4.0 represents the convergence of digital technologies with manufacturing processes, enabling smart factories that are more interconnected, data-driven, and automated than ever before. In the context of CNC drilling machines, the transition to Industry 4.0 has resulted in machines that can operate autonomously, optimize their own processes, and communicate seamlessly with other devices and systems. This has major implications for businesses in the Netherlands that rely on CNC drilling machines for high-precision drilling applications.
The rapid adoption of Industry 4.0 technologies is helping manufacturers reduce downtime, improve production rates, and ensure higher-quality products. Furthermore, the integration of these technologies into CNC drilling machines allows companies to scale up production without compromising on quality or precision.
Automation in CNC Drilling Machines
Automation is at the core of Industry 4.0, and it is one of the primary driving forces behind the changes in the Netherlands CNC drilling machine market. Modern CNC drilling machines are designed to perform complex tasks with minimal human intervention, which has greatly increased the efficiency of manufacturing processes.
Automated CNC machines are capable of performing repetitive tasks without fatigue, ensuring consistent performance throughout long production runs. This reduction in human error leads to improved product quality, fewer defects, and a faster time to market. In the Netherlands, many manufacturers are upgrading their drilling machines to automated models, which can run 24/7 with minimal supervision, reducing labor costs and increasing overall productivity.
Additionally, automation in CNC drilling machines enables faster adaptation to production changes. As demand for custom products and smaller production batches rises, the ability to reprogram CNC machines quickly and efficiently is crucial. Automated systems can quickly adjust drilling operations to accommodate new designs and specifications, making the process more agile and adaptable to market demands.
IoT Integration and Smart CNC Drilling Machines
The Internet of Things (IoT) has revolutionized manufacturing by enabling machines to connect and communicate with each other and with central control systems. IoT-enabled CNC drilling machines in the Netherlands are now capable of exchanging data in real time, allowing manufacturers to monitor and optimize production processes more effectively.
With IoT integration, CNC drilling machines can collect data on machine performance, tool wear, and environmental conditions. This data can be sent to cloud-based platforms or directly to operators, enabling real-time monitoring and predictive maintenance. Manufacturers can use this data to schedule maintenance before a failure occurs, preventing costly downtime and extending the lifespan of their drilling equipment.
The ability to collect and analyze data from CNC drilling machines also allows businesses in the Netherlands to optimize their production processes. IoT technology enables manufacturers to fine-tune machine parameters, adjust speed and feed rates, and monitor energy consumption, leading to more efficient and sustainable operations.
Moreover, IoT devices allow remote monitoring of CNC drilling machines, enabling operators and engineers to diagnose issues and make adjustments from anywhere in the world. This level of connectivity provides businesses with greater flexibility and control over their production processes.
AI and Machine Learning in CNC Drilling Machines
Artificial Intelligence (AI) and machine learning are pushing the boundaries of what CNC drilling machines can achieve in terms of automation, precision, and decision-making. AI algorithms are capable of analyzing vast amounts of data to identify patterns and optimize machine performance in real time.
In the Netherlands CNC drilling machine market, AI-powered machines are becoming increasingly common. These machines can learn from past production runs and continuously adjust drilling parameters for optimal results. By analyzing data from multiple sensors, AI can detect subtle variations in material properties or tool wear and automatically adjust drilling parameters to compensate for these changes.
AI is also making it possible to create self-optimizing CNC drilling systems. These systems use machine learning algorithms to automatically adjust drilling speeds, tool paths, and other parameters to maximize efficiency and reduce waste. As a result, businesses can achieve higher levels of precision while minimizing energy consumption and material waste.
One of the most exciting developments in AI for CNC drilling machines is the potential for autonomous decision-making. In the future, AI algorithms may be able to independently choose the best tools and techniques for a specific task, enabling fully autonomous CNC drilling operations. This would further reduce the need for human intervention and increase operational efficiency.
Benefits of Industry 4.0 for the Netherlands CNC Drilling Machine Market
The integration of Industry 4.0 technologies into CNC drilling machines brings numerous benefits to manufacturers in the Netherlands. Here are some of the key advantages:
1. Increased Efficiency: Automation, IoT, and AI enable CNC drilling machines to operate at higher speeds and greater precision. These technologies also reduce the need for manual intervention, allowing machines to run continuously without breaks, which increases overall production capacity.
2. Enhanced Precision: AI and IoT sensors can monitor and adjust drilling operations in real time, ensuring that each hole is drilled with the utmost accuracy. This is particularly important for industries like aerospace and automotive, where precision is crucial.
3. Predictive Maintenance: By collecting data from CNC drilling machines, manufacturers can predict when a machine is likely to fail or when a tool needs to be replaced. This proactive approach to maintenance reduces unplanned downtime and lowers maintenance costs.
4. Cost Reduction: Automation and AI reduce labor costs, and IoT-based predictive maintenance can prevent expensive repairs. Additionally, AI can help optimize production processes, minimizing material waste and energy consumption, further driving cost savings.
5. Flexibility and Customization: The ability to easily reprogram CNC machines makes it easier to accommodate custom orders and smaller batch sizes. Manufacturers in the Netherlands can quickly switch between different production runs without significant downtime.
6. Improved Sustainability: IoT integration allows manufacturers to monitor energy usage and optimize machine settings to reduce consumption. By minimizing waste and improving energy efficiency, the CNC drilling machine market in the Netherlands is moving toward more sustainable manufacturing practices.
Challenges in Adopting Industry 4.0 in CNC Drilling Machines
Despite the numerous benefits, the transition to Industry 4.0 comes with its own set of challenges. Some of the obstacles that manufacturers in the Netherlands may face when adopting these advanced technologies include:
1. High Initial Investment: The cost of upgrading to smart CNC drilling machines that incorporate automation, IoT, and AI can be significant. Small and medium-sized businesses may find it challenging to justify these upfront costs, despite the long-term savings.
2. Skilled Labor Shortages: As machines become more advanced, there is a growing need for workers with specialized skills in programming, data analysis, and machine learning. Training employees to work with these new technologies may require significant investment in education and development.
3. Cybersecurity Risks: The increased connectivity brought by IoT devices creates potential vulnerabilities in cybersecurity. Manufacturers must ensure that their systems are secure from cyber threats to protect sensitive data and avoid disruptions to their operations.
4. Integration Complexity: Integrating new technologies with legacy systems can be complex and time-consuming. Manufacturers may need to invest in additional software or infrastructure to ensure smooth communication between different machines and platforms.
Future Outlook for the Netherlands CNC Drilling Machine Market
The future of the Netherlands CNC Drilling Machine Market looks promising as Industry 4.0 continues to evolve. As AI, IoT, and automation become more integrated into CNC drilling machines, manufacturers in the Netherlands will see even greater advancements in efficiency, precision, and customization. The adoption of smart manufacturing practices is expected to increase, driving competitiveness and boosting the economy.
Additionally, the increasing demand for sustainable manufacturing practices will encourage the adoption of energy-efficient and waste-reducing technologies in CNC drilling machines. The market will likely see the development of more advanced AI systems capable of autonomous decision-making and self-optimization.
Conclusion
The Netherlands CNC Drilling Machine Market is undergoing a remarkable transformation driven by Industry 4.0 technologies. Automation, IoT, and AI are redefining the capabilities of CNC drilling machines, enabling businesses to achieve greater efficiency, precision, and sustainability. As the manufacturing sector continues to embrace these innovations, the Dutch market will undoubtedly remain at the forefront of precision manufacturing, offering a competitive edge to businesses across various industries. By overcoming challenges such as high initial investment costs and the need for skilled labor, manufacturers can unlock the full potential of these technologies, positioning themselves for long-term success in an increasingly digital world.
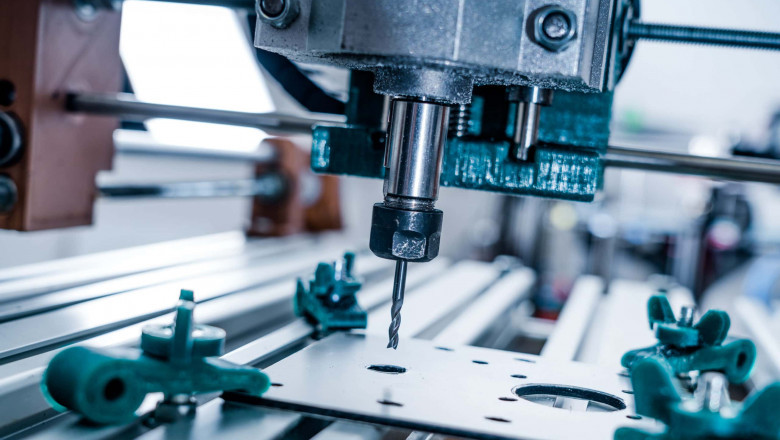
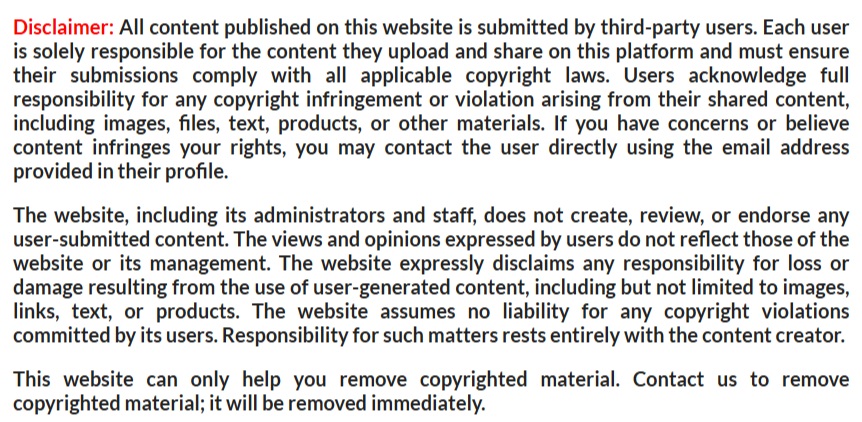
Comments
0 comment