views
Automotive and aerospace precision turned parts are critical to the accuracy, dependability, and overall performance of devices where these aspects are critical. They require tight tolerances and flawless surface finishes as these imperfections cause moisture to seep through and would end up creating mechanical failures or safety hazards. Turned parts basically include shafts, bushings, and fasteners which are integral components of engine systems, suspension, and transmission in automotives. Precision turned fasteners such as connectors, spacers, and fittings withstand high pressure, temperature, and vibration in an aircraft. These are all produced by CNC turning and thus these parts are made with high-level precision, ensuring that they meet the conditions of very harsh industry standards and certifications. With advance in technology, the need for light weight, high strength, and complex turned components continue to grow, thereby proving their significance toward current modern mobility solutions.
Turned vs Milled Components: Major Differences and Differences Explained
Turned parts and milled components both find abundant applicability in precision engineering, but their methods of manufacturing, use, and geometrical representations differ significantly. While turned components are produced through CNC turning-an operation in which the workpiece rotates against a stationary cutting tool-they are highly used for producing cylindrical or symmetrical shapes like shafts, bushings, and pins. Unlike the milling process where the cutting tool rotates on a stationary workpiece, the actual component would not be moving at all; rather, it is stationary, allowing the creation of complex shapes and surfaces-(flat and angular) such as brackets, housings, and slots. So generally understood, turning gives you speed and precision for round parts; for flat profiles or complex designs with many surfaces, milling is your answer. With this kind of information, manufacturers will be able to easily determine which turning or milling approach is applicable and best for them based on part geometry, tolerance needs, and production volume.
Role of Turned Components in Improving Indication Performance of Industrial Machines
Turned component manufacturer create a vital role in the focusing performance of industrial machinery. These high-speed operational components such as shafts, spindles, couplings, bushings, etc. are under consideration on continuous motion, heavy loads, and high speeds. Such Precision components eliminate the friction and also keep them aligned for smooth mechanical movement with all high-speed and heavy industrial use of requirement available through CNC turning of tight tolerances and very smooth surface finishes. In other words, this means less wear and tear, improved energy efficiency, and reduced downtime and lost production. The use of superior quality turned parts helps the manufacturers in achieving a longer effective life of equipment, constant output, and low maintenance costs, which becomes a prime feature for keeping productivity and performance alive in several industrial applications.
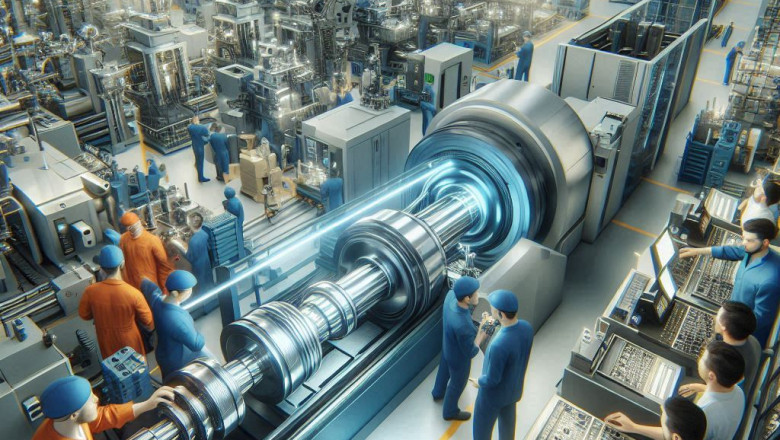
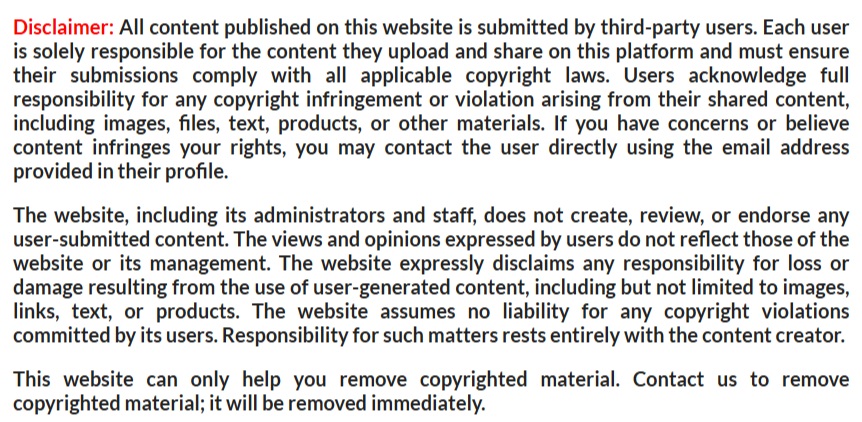
Comments
0 comment