views
Composition and Properties of EPDM Rubber
EPDM rubber is a terpolymer consisting of ethylene, propylene, and a non-conjugated diene monomer. The ethylene and propylene monomers provide the rubbery characteristics, while the diene units allow for vulcanization of the polymer through sulfur and peroxide curing systems. Common dienes used are ethylidene norbornene (ENB) and dicyclopentadiene (DCPD). The ratio of ethylene to propylene can be varied to tailor the properties of the rubber. Higher ethylene content increases flexibility and elastometric recovery, while more propylene provides greater resistance to oil, chemicals and heat. Through controlled polymerization, EPDM can be engineered to have a very wide range of physical and performance properties.
Production Processes for EPDM
Ethylene Propylene Diene Monomer (Epdm) is polymerized in a solution or slurry process using Ziegler-Natta or metallocene catalysts. For solution polymerization, the monomers are dissolved in an organic solvent under high pressures and temperatures in the presence of catalysts. Hexane and cyclohexane are commonly used as solvents. In slurry polymerization, the monomers are suspended in a liquid medium rather than fully dissolved. This allows for higher productivities but requires more complex extraction of the rubber from the slurry. The manufactured EPDM is separated from the solvent or slurry and may undergo further compounding processes like mixing in fillers, plasticizers and vulcanizing agents.
Major Applications of EPDM Rubber
Automotive parts represent a huge application area for EPDM due to requirements for heat resistance, oil resistance and weatherability. Common automotive rubber applications include hoses, belts, seals and gaskets. Construction sealants and weatherstripping also capitalize on EPDM's resilience and durability against UV light and moisture. Its low permeability to gases like oxygen and moisture make it well-suited for roofing membranes and pond liners. EPDM is widely used as insulating materials for wire and cable due to good dielectric properties both at low and high voltages. Other niche uses include oil additives, adhesives and footwear.
Vulcanization and Compounding of EPDM
EPDM powder or pellets are mixed with other ingredients prior to vulcanization into a finished product. Carbon black or mineral fillers are added to improve mechanical properties and heat resistance. Plasticizers enhance flexibility and processing, with paraffinic and naphthenic oils being typical. Sulfur or peroxide-based curing agents initiate crosslinking of polymer chains during vulcanization. Zinc oxide, stearic acid and accelerators aid the curing process. Additional compounding agents may include anti-oxidants, UV absorbers, pigments and flame retardants depending on the specific formulation. Cured EPDM products can have a wide range of physical properties tuned towards varying applications.
Testing and Quality Control of EPDM Rubber
Manufacturers subject EPDM rubber samples to rigorous testing at different production stages to ensure consistency and compliance with standards. Key physical properties evaluated include tensile strength, elongation at break, hardness/durometer, density, compression set and resilience. Tests are also conducted for resistance to ozone, weathering, fluids, chemicals, heat and fire. Analytical techniques like FTIR spectroscopy, DSC, DMA and SEM are employed to characterize polymer microstructure and crosslinking. Quality control involves statistical process monitoring through automated testing equipment. Finished EPDM goods need to adhere to product specifications and satisfy customer requirements based on relevant ASTM, ISO, UL, IEC standards as applicable. Proper quality assurance leads to enhanced performance reliability of EPDM formulations.
Growing Demand for EPDM in Developing Markets
The global EPDM market was valued around USD 4.5 billion in 2019 and has been projected to grow at over 5% annually through 2027. Growth is driven by increasing construction activities and infrastructure developments in emerging economies. Asia Pacific currently dominates EPDM consumption due to large automotive, wire and cable sectors in China and India. Regulations mandating use of non-asbestos gaskets and hoses have also augmented rubber requirement. Other rapidly industrializing nations in Southeast Asia, Middle East and Africa are raising demand. Manufacturers are expanding EPDM production capacities and custom rubber compounding plants across developing markets to capitalize on rising local needs. The versatile properties of EPDM continue making it a material of choice for various weatherproofing and sealing solutions globally.
Environmental and Sustainability Issues
Like most elastomers, disposal and incineration of EPDM waste generates air emissions and leachates. Incomplete combustion releases particulates, metals, dioxins and furans harmful to ecosystems and human health if not disposed properly. Reclaimed EPDM faces challenges due to black carbon and filler contamination from prior formulations. Research efforts are examining chemical and thermal recycling technologies to recover ethylene, propylene and other monomers from waste rubber. Use of green plasticizers and bio-based fillers is being explored to make compounding more sustainable. Some manufacturers offer take-back programs and strive for greater recycling rates of post-industrial and post-consumer EPDM. Adoption of greener processing methods and stringent emission norms will be critical to mitigate environmental footprint of the booming rubber industry.
Get this Report in Japanese Language:
Get this Report in Korean Language:
About Author:
Money Singh is a seasoned content writer with over four years of experience in the market research sector. Her expertise spans various industries, including food and beverages, biotechnology, chemical and materials, defense and aerospace, consumer goods, etc. (https://www.linkedin.com/in/money-singh-590844163)
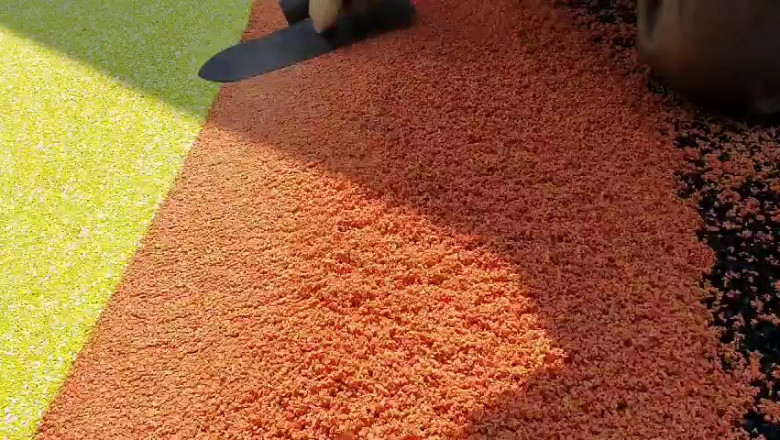

Comments
0 comment