views
Dialysis kits are critical medical products used in the management of kidney failure, enabling patients to filter waste, toxins, and excess fluids from their blood. These kits are essential for both haemodialysis and peritoneal dialysis procedures, ensuring patient safety and treatment efficiency. With the growing prevalence of chronic kidney diseases and the increasing demand for high-quality healthcare solutions, the dialysis kit market has seen significant growth. Establishing a manufacturing plant for dialysis kits involves stringent quality control, advanced production methods, and adherence to medical safety standards. This article provides an in-depth guide to setting up a successful dialysis kit manufacturing facility.
Understanding Dialysis Kits
Dialysis kits are comprehensive medical packages that include all necessary components for conducting dialysis. These typically consist of dialysers, tubing sets, catheters, and sterile solutions. Designed for single-use or reusable purposes, dialysis kits ensure efficient treatment and minimise infection risks.
Get a Free Sample Report with Table of Contents@ https://www.expertmarketresearch.com/prefeasibility-reports/dialysis-kit-manufacturing-plant-project-report/requestsample
Key Processes in Manufacturing
- Raw Material Procurement
- Materials like medical-grade plastics, membranes, and sterile solutions are sourced from certified suppliers. These materials undergo stringent quality checks to ensure compliance with safety standards.
- Component Fabrication
- Key components such as tubing, connectors, and membranes are manufactured using processes like extrusion, moulding, and casting.
- Assembly
- The fabricated components are assembled into complete kits, ensuring proper integration and functionality. Automation can enhance precision and efficiency during this stage.
- Sterilisation
- Assembled kits are sterilised using methods like ethylene oxide gas or gamma radiation to eliminate microbial contamination.
- Packaging
- The sterilised kits are packaged in airtight, tamper-proof pouches to maintain sterility. Packaging includes clear labelling and usage instructions.
- Quality Testing
- Each batch of dialysis kits undergoes rigorous testing for durability, sterility, and compatibility to meet medical industry standards.
- Storage and Distribution
- Packaged products are stored in controlled environments and distributed to healthcare facilities, dialysis centres, and pharmacies.
Essential Equipment for a Manufacturing Plant
Setting up a dialysis kit manufacturing plant requires advanced machinery and infrastructure for efficient and safe production. Key equipment includes:
- Injection Moulding Machines: For producing plastic components such as tubing and connectors.
- Extrusion Machines: For creating high-quality medical-grade tubing.
- Sterilisation Units: For eliminating microbial contamination from the assembled kits.
- Assembly Lines: For integrating components into complete kits.
- Packaging Machines: For sealing and labelling the finished products.
- Quality Testing Instruments: For assessing durability, sterility, and performance.
Designing the Plant Layout
An efficient plant layout ensures smooth operations and compliance with hygiene standards. Key considerations include:
- Raw Material Storage: Secure areas for storing medical-grade materials.
- Processing Zones: Separate sections for moulding, assembly, and sterilisation.
- Quality Control Laboratory: Equipped for testing raw materials and finished products.
- Packaging and Labelling Areas: Automated systems for sealing and branding dialysis kits.
- Storage Facilities: For maintaining optimal conditions to preserve the packaged kits.
Quality Control in Manufacturing
Maintaining consistent quality is crucial for dialysis kit production. Key quality control practices include:
- Raw Material Testing: Verifying the compatibility and safety of medical-grade plastics and membranes.
- Process Monitoring: Ensuring precise manufacturing and assembly techniques.
- Product Testing: Assessing sterility, functionality, and durability of the kits.
- Packaging Inspection: Checking for airtight seals and accurate labelling.
Regulatory and Licensing Requirements
Establishing a dialysis kit manufacturing plant involves compliance with stringent medical and safety regulations. Key requirements include:
- Medical Device Certifications: Adherence to ISO 13485 or similar standards for medical device manufacturing.
- Labelling Compliance: Providing clear usage instructions, warnings, and batch details.
- Sterility Validation: Ensuring all products meet sterility requirements through approved testing methods.
- Workplace Safety Regulations: Ensuring safe handling of materials and machinery to protect workers.
Applications of Dialysis Kits
Dialysis kits are essential in the treatment of kidney failure and chronic kidney diseases. Key applications include:
- Healthcare Facilities: Used in hospitals and clinics for both haemodialysis and peritoneal dialysis.
- Home Dialysis: Kits designed for patients undergoing treatment at home.
- Emergency Medical Use: Portable dialysis kits for use in emergency or temporary settings.
- Research and Training: Used in medical research and training centres for simulation and study purposes.
Sustainability in Manufacturing
Sustainability is an important consideration in dialysis kit production. Key measures include:
- Eco-Friendly Materials: Using biodegradable or recyclable plastics where feasible.
- Waste Management: Implementing systems for the safe disposal of medical waste.
- Energy Efficiency: Employing energy-saving technologies in sterilisation and production processes.
- Minimal Packaging: Using recyclable or biodegradable materials for product packaging.
Market Trends and Opportunities
The dialysis kit market is expanding due to the rising prevalence of chronic kidney diseases and advancements in medical technology. Key trends include:
- Increased Home Dialysis Adoption: Rising demand for portable and user-friendly dialysis kits.
- Focus on Single-Use Kits: Increased preference for single-use kits to minimise infection risks.
- Global Expansion: Growing adoption in emerging markets with improved healthcare access.
- Technological Advancements: Development of innovative kits with enhanced functionality and safety features.
Challenges in the industry include:
- Raw Material Costs: Managing fluctuations in the prices of medical-grade materials.
- Regulatory Compliance: Meeting stringent safety and sterility standards.
- Market Competition: Differentiating products through innovation and superior quality.
By adopting advanced production techniques, ensuring stringent quality control, and focusing on sustainability, manufacturers can establish a successful dialysis kit production facility to cater to the growing global demand for efficient and reliable medical devices.
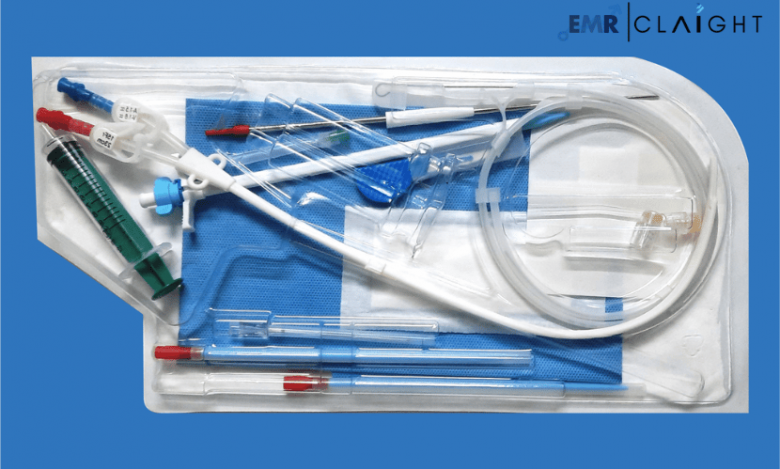
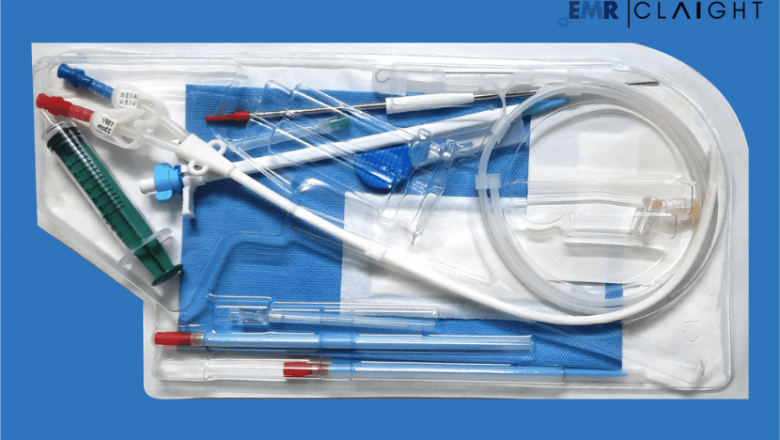

Comments
0 comment