views
Aerospace coatings play a vital role in protecting aircraft from harsh environmental conditions like extreme heat, cold, rain, corrosion, and solar radiation. These coatings help aircraft components maintain their structural integrity and perform efficiently throughout their operational life. Let's understand the different types and key functions of aerospace coatings.
Types of Aerospace Coatings
Primers: Primers form the first layer of any coating system. Aerospace Coating provide corrosion protection and improve adhesion between the substrate and topcoats. Epoxy and polyurethane are some commonly used primer materials.
Topcoats: Topcoats are applied over primers to provide the final layer of protection. Some common topcoat varieties include:
- Epoxy topcoats: Durable and chemical resistant, epoxy topcoats protect against corrosion and abrasion.
- Polyurethane topcoats: Tough and flexible, polyurethane topcoats provide UV protection and glare reduction.
- Sol-gel topcoats: Very lightweight and transparent, sol-gel topcoats are used on canopies and windshields.
Specialty coatings: In addition to primers and topcoats, specialty coatings are used for specific purposes like lightning strike protection, chemical resistance in undercarriages, and thermal barrier coatings for hot sections.
Functions of Aerospace Coatings
Corrosion Protection: Aerospace coatings form a physical barrier to protect metal surfaces from corrosion caused by moisture, chemicals, ultraviolet light, and other environmental factors. This helps extend the lifespan of aircraft structures.
Abrasion Resistance: The top layers ensure coated parts can withstand abrasion from debris, dust, rain erosion, and other abrasive particles encountered during operations.
Condition Monitoring: Some advanced intelligent coatings have sensors embedded in them to monitor the health of aircraft structures and components in real-time.
Weight Savings: Specialized lightweight coatings reduce the overall weight of aircraft, allowing for greater payloads and fuel efficiency. Sol-gel coatings are prime examples.
Heat Resistance: Thermal barrier coatings enable aircraft components like jet engines to tolerate extremely high temperatures during flight. This boosts performance.
Coating Application and Curing Processes
There are various application techniques used for aerospace coatings depending on the part geometry and coating material properties:
Dip Coating: Used for simple shaped parts which are dipped into a tank of liquid coating. It allows full coverage but uses more material.
Spray Coating: The most versatile technique where coatings in liquid, powder or dispersion form are sprayed onto parts using air or airless spray guns.
Electrostatic Spray Coating: Applying an electrostatic charge to liquid spray improves transfer efficiency and reduces overspray. Used for large assemblies.
Brush/Roller Coating: Manual method suitable for smaller parts or those with restricted spray access. Provides uniform film building.
After application, coatings need to undergo curing processes to develop their final protective properties. Thermal curing using ovens is common for epoxy and polyurethane coatings where the part is baked at elevated temperatures. UV curing involves exposing the wet coating to ultraviolet light for rapid solidification.
Quality Assurance and Testing
Extensive quality control measures and testing are essential for certified aircraft coatings. This ensures the chosen coating system will protect components reliably throughout their design service life.
Some key tests performed on aerospace coatings include:
Adhesion Testing: Tests the bond strength of coatings to substrates using cross-hatch or pull-off tests.
Corrosion Testing: Exposes coated samples to corrosive environments like salt spray to evaluate protection.
Abrasion Resistance Testing: Measures wear using abrasive wheels, sand, and erasers under controlled conditions.
Weathering Testing: Subjects coatings to prolonged sunlight exposure, humidity cycling, and other weather simulations.
Regulatory standards like AMS 3270 from SAE International specify pass/fail acceptance criteria for various tests aerospace coatings must undergo. Only those meeting the critical performance requirements get qualified for use.
With aircraft operating under extreme climatic challenges, effective protection of airframe structures and propulsion components through specialized coatings is indispensable. Today’s advanced coatings help manufacturers design stronger, lighter and more durable aircraft with lower life cycle costs. Continued advancements will certainly make future aircraft coatings even more multifunctional and intelligent.
Get This Report in Japanese Language: 航空宇宙コーティング
Get This Report in Korean Language: 항공우주 코팅
About Author:
Vaagisha brings over three years of expertise as a content editor in the market research domain. Originally a creative writer, she discovered her passion for editing, combining her flair for writing with a meticulous eye for detail. Her ability to craft and refine compelling content makes her an invaluable asset in delivering polished and engaging write-ups.
(LinkedIn: https://www.linkedin.com/in/vaagisha-singh-8080b91)
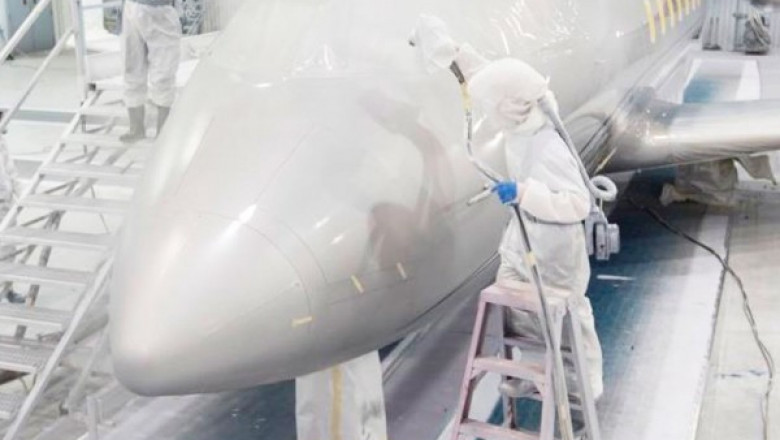

Comments
0 comment