views
The rigid sleeve box market has seen significant advancements driven by technological innovations and evolving consumer demands. These innovations not only improve the functionality of the boxes but also enhance their aesthetic appeal, sustainability, and overall efficiency in the packaging industry. This article highlights key innovations and technological advancements that are shaping the rigid sleeve boxes market.
1. Digital Printing and Customization
Digital printing has revolutionized the design and customization capabilities for rigid sleeve boxes. It allows for more intricate and detailed designs that are cost-effective and can be produced quickly.
- High-Quality Print: Digital printing enables brands to create sharp, high-resolution designs on rigid sleeve boxes. This is ideal for brands that want to include detailed graphics, logos, and other intricate visual elements.
- Cost-Effective Short Runs: Digital printing allows for smaller production runs without incurring high setup costs, making it ideal for businesses that require low-volume, custom packaging.
- Full-Color Designs: Brands can now print vibrant, full-color designs, improving the overall appearance and visual appeal of rigid sleeve boxes.
2. Sustainable Material Innovations
As consumer and regulatory pressures for sustainability increase, the rigid sleeve box market is shifting towards more eco-friendly materials. Manufacturers are exploring new ways to reduce the environmental impact of packaging through sustainable sourcing and material innovation.
- Recyclable and Biodegradable Materials: The use of materials such as recycled cardboard, paperboard, and biodegradable plastics is becoming more widespread. These materials offer the durability of traditional packaging while reducing environmental harm.
- Plant-Based Inks: The use of eco-friendly, plant-based inks in the printing process has reduced the use of harmful chemicals, further contributing to the sustainability of rigid sleeve boxes.
- Reduced Material Waste: Advances in material engineering are enabling manufacturers to create packaging with less material waste, improving resource efficiency.
3. Automation and Smart Manufacturing
Automation is transforming the production of rigid sleeve boxes, making it faster, more efficient, and cost-effective. Through automated manufacturing processes, businesses can increase throughput while maintaining high-quality standards.
- Automated Cutting and Assembly: Automated cutting machines and assembly lines allow for faster production times and more precise cutting, ensuring that the rigid sleeve boxes meet the required specifications.
- Robot-Assisted Packaging: Robotic arms are being employed to handle and package rigid sleeve boxes with speed and precision, reducing human error and increasing production efficiency.
- Real-Time Monitoring: Smart manufacturing systems allow for real-time monitoring of production processes, ensuring that any issues are addressed immediately and production continues smoothly.
4. Smart Packaging Features
The rigid sleeve box market is also benefiting from the integration of smart packaging technologies, which enhance the functionality and user experience of the packaging.
- RFID and QR Codes: Radio-frequency identification (RFID) tags and QR codes are becoming common additions to rigid sleeve boxes, providing businesses with improved inventory tracking, supply chain management, and consumer engagement. By scanning QR codes, consumers can access product information, promotions, or even interactive content.
- Temperature Sensors: In industries such as food and pharmaceuticals, temperature-sensitive rigid sleeve boxes with built-in temperature sensors are ensuring that products maintain the right conditions during shipping and storage.
- Interactive Packaging: Augmented reality (AR) and interactive features are increasingly being incorporated into rigid sleeve boxes, allowing consumers to engage with the packaging in new ways. For example, AR-enabled packaging can bring a product’s story to life, enhancing the unboxing experience.
5. Improved Protection Features
Technological advancements have also enhanced the protective capabilities of rigid sleeve boxes, making them more suitable for high-end products that require extra care during handling and shipping.
- Impact-Resistant Materials: The use of stronger, more resilient materials has improved the protective qualities of rigid sleeve boxes. These materials can withstand impacts, ensuring that products inside remain safe during transit.
- Foam Inserts and Cushioning: Rigid sleeve boxes are increasingly featuring custom foam inserts, dividers, and other protective cushioning materials to prevent product damage. These inserts not only provide additional protection but also enhance the luxury feel of the packaging.
6. Custom Shape and Size Innovations
With the demand for unique and eye-catching packaging solutions, manufacturers are increasingly experimenting with custom shapes and sizes for rigid sleeve boxes. This innovation is particularly popular in luxury packaging, where distinct, non-standard shapes can significantly enhance the product’s appeal.
- Non-Traditional Shapes: Rigid sleeve boxes are no longer limited to rectangular or square designs. Brands are exploring more innovative shapes, including hexagonal, triangular, and even irregular forms, to stand out in the marketplace.
- Flexible Sizing: Advances in design software and production techniques allow for greater flexibility in the size of rigid sleeve boxes, enabling packaging solutions tailored to specific product dimensions.
7. Enhanced Finishing Techniques
In response to growing demand for premium and aesthetically pleasing packaging, there have been significant advancements in finishing techniques for rigid sleeve boxes. These finishes add an extra layer of sophistication and appeal to the packaging.
- Embossing and Debossing: Embossing and debossing techniques allow for raised or recessed designs, adding texture and tactile appeal to the rigid sleeve boxes. This enhances the visual impact and makes the packaging feel more luxurious.
- Foil Stamping: Foil stamping with metallic or holographic foil adds a shiny, high-end effect to rigid sleeve boxes, making them more eye-catching and desirable, particularly in the luxury goods sector.
- Matte and Gloss Coatings: Advanced matte and gloss coatings give packaging a more refined finish, catering to different brand aesthetics. Matte finishes provide a more subtle and elegant look, while glossy coatings enhance the vibrancy of printed designs.
8. 3D Modeling and Prototyping
The introduction of 3D modeling and prototyping has accelerated the development of rigid sleeve boxes, enabling manufacturers to test designs and make necessary adjustments before going into full production.
- Rapid Prototyping: Manufacturers can now create prototypes of rigid sleeve boxes using 3D printing, allowing for quicker iterations and reducing the time and cost associated with physical samples.
- Enhanced Design Accuracy: 3D modeling tools allow for more precise and intricate designs, ensuring that manufacturers can achieve the desired final look and functionality without the need for costly revisions.
Final Thoughts
Innovations and technological advancements are driving the evolution of the rigid sleeve boxes market, making packaging more sustainable, efficient, and customizable. From digital printing and eco-friendly materials to automation and smart packaging, these innovations are enabling brands to enhance their packaging while meeting the growing demand for sustainability and customization. As the market continues to evolve, embracing new technologies will be crucial for manufacturers to stay competitive and meet the expectations of both consumers and businesses.
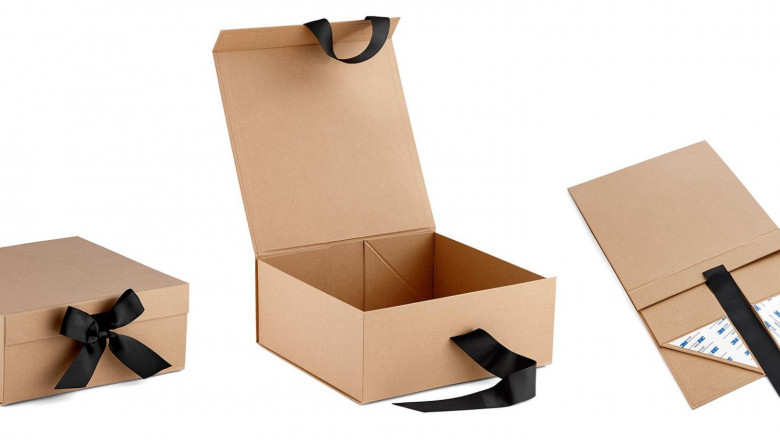

Comments
0 comment