views
The Gasketed Heat Exchangers Market has seen remarkable growth over the years, particularly in industries where cleanliness, safety, and energy efficiency are paramount. One such industry where these attributes are critical is the food and beverage processing sector. In this article, we will explore the key role gasketed heat exchangers play in the food and beverage industry, focusing on hygiene standards, safety regulations, and energy efficiency.
Introduction to Gasketed Heat Exchangers
A gasketed heat exchanger is a type of heat exchanger that utilizes gaskets between plates to facilitate the transfer of heat between two fluids. These exchangers are widely used in various industries, including food and beverage processing, pharmaceuticals, and chemical manufacturing, due to their ability to maintain high levels of efficiency and hygiene.
In food and beverage processing, heat exchangers are indispensable for processes like pasteurization, sterilization, and cooling, ensuring that products are safe for consumption while maintaining their quality. Gasketed heat exchangers are particularly preferred in this sector due to their ease of maintenance, efficient heat transfer properties, and flexibility in design.
Hygiene Standards in Food & Beverage Processing
Hygiene is a non-negotiable requirement in food and beverage processing. Contaminants and microorganisms can easily thrive in food products, compromising their safety and shelf-life. For this reason, maintaining stringent hygiene standards is vital to prevent foodborne illnesses and ensure product quality.
Gasketed heat exchangers are designed to meet the stringent hygiene standards required in the food and beverage industry. Their smooth, easy-to-clean surfaces reduce the risk of bacterial growth, which can occur in areas with difficult-to-clean joints and welds. The plate design of these heat exchangers allows for a large surface area for heat exchange, while the gaskets ensure a tight seal to prevent cross-contamination between the fluids.
In addition, the gaskets used in these heat exchangers are made from food-grade materials such as EPDM (ethylene propylene diene monomer) and NBR (nitrile butadiene rubber), which are non-toxic and resistant to chemical degradation. These materials ensure that no harmful substances leach into the product during the heat exchange process.
Safety Standards in Food & Beverage Processing
In the food and beverage industry, safety is a top priority. This includes both the safety of the workers operating the machinery and the safety of the end consumer. Food products must be processed in a way that eliminates any potential hazards, including microbial contamination, while also ensuring that the process is safe for workers.
Gasketed heat exchangers play a critical role in ensuring safety within the food and beverage sector. One key advantage of gasketed heat exchangers is their ability to operate at high temperatures and pressures without compromising the integrity of the system. This is essential for processes like pasteurization, where high temperatures are required to kill harmful pathogens in food products.
The design of gasketed heat exchangers also ensures a high level of safety for workers. The compact and modular design of these exchangers makes them easy to maintain and clean, reducing the risk of exposure to potentially harmful chemicals or microbes. Moreover, the gaskets create a seal that prevents leaks, reducing the likelihood of fluid spills and accidents.
Energy Efficiency in Food & Beverage Processing
Energy efficiency is a key concern in modern food and beverage processing. Rising energy costs and increased pressure to reduce environmental impact have driven the adoption of more energy-efficient technologies across all sectors. Gasketed heat exchangers have proven to be a highly effective solution in this regard.
These heat exchangers are designed for maximum heat transfer efficiency, which helps minimize energy consumption. By optimizing the heat transfer process, gasketed heat exchangers reduce the need for additional energy inputs, leading to significant savings in operating costs. Additionally, their compact design allows for better space utilization, making them suitable for a wide range of processing plants, from small-scale operations to large industrial facilities.
Furthermore, gasketed heat exchangers can be used in combination with energy recovery systems, which enable the reuse of excess heat from one process for another. This not only improves overall energy efficiency but also contributes to a more sustainable processing environment.
The Role of Gasketed Heat Exchangers in Pasteurization
One of the most common applications of gasketed heat exchangers in the food and beverage industry is in pasteurization. This process involves heating food products to a specific temperature for a set period to kill harmful microorganisms without compromising the quality of the product. Gasketed heat exchangers are ideal for pasteurization because they provide efficient heat transfer while maintaining hygienic conditions.
By using gasketed heat exchangers in pasteurization, food processors can ensure that products are consistently heated to the required temperatures, effectively killing pathogens while preserving the nutritional content and flavor. The ability to control temperatures precisely also minimizes energy waste, making the pasteurization process more efficient.
Flexibility and Customization of Gasketed Heat Exchangers
The food and beverage industry is diverse, with varying requirements depending on the type of product being processed. Gasketed heat exchangers offer a high degree of flexibility, allowing manufacturers to tailor the equipment to their specific needs.
For example, gasketed heat exchangers can be designed with multiple plates and customized gaskets to accommodate different flow rates, pressures, and temperatures. This flexibility makes them suitable for a wide range of food products, from dairy and beverages to sauces and ready-to-eat meals.
Sustainability and Environmental Benefits of Gasketed Heat Exchangers
As sustainability becomes an increasingly important factor in the food and beverage industry, gasketed heat exchangers contribute by minimizing energy usage and reducing environmental impact. Their efficient heat transfer capabilities reduce the need for additional energy inputs, which helps lower carbon emissions. Moreover, the modular design of gasketed heat exchangers allows for easy upgrades and retrofits, ensuring that processing plants can stay up-to-date with the latest energy-efficient technologies.
Challenges in the Gasketed Heat Exchanger Market
Despite their many advantages, gasketed heat exchangers face some challenges, particularly in terms of material degradation over time. The gaskets used in these exchangers can wear out due to constant exposure to high temperatures and pressures, which can lead to leaks and potential contamination. Regular maintenance and replacement of gaskets are crucial to ensuring the continued performance and hygiene standards of the system.
Additionally, the initial cost of gasketed heat exchangers can be relatively high compared to other types of heat exchangers. However, the long-term benefits, including reduced energy consumption, lower maintenance costs, and improved hygiene and safety standards, make them a cost-effective solution in the long run.
Future Outlook for the Gasketed Heat Exchanger Market
The gasketed heat exchanger market is expected to continue growing in the coming years, driven by increasing demand for energy-efficient, safe, and hygienic solutions in food and beverage processing. As the food industry continues to prioritize sustainability and safety, gasketed heat exchangers will play an essential role in meeting these evolving needs.
Advances in materials science are likely to improve the performance and longevity of gaskets, reducing the frequency of replacements and enhancing the overall reliability of these heat exchangers. Furthermore, innovations in design and technology will continue to drive efficiencies, making gasketed heat exchangers even more adaptable and cost-effective for food processors.
Conclusion
In conclusion, gasketed heat exchangers are a critical component in modern food and beverage processing. They help maintain stringent hygiene and safety standards, while also contributing to energy efficiency and sustainability. As the industry continues to evolve, gasketed heat exchangers will remain a vital tool in ensuring that food products are safe, high-quality, and produced with minimal environmental impact.
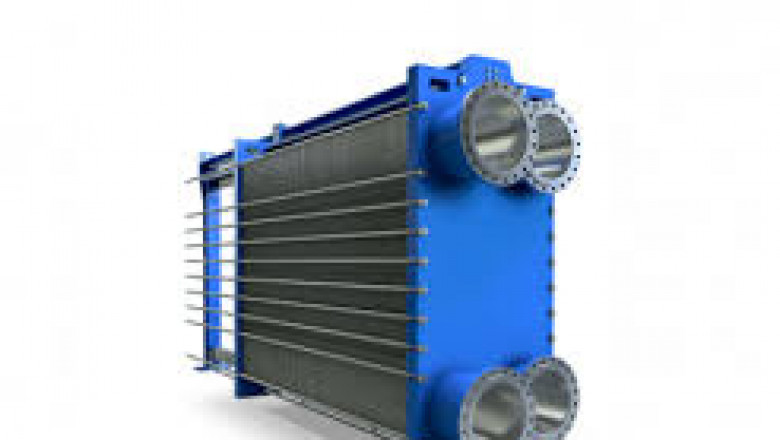

Comments
0 comment