views
Introduction
Thailand is rapidly emerging as a significant hub for electric vehicle (EV) manufacturing in Southeast Asia. With ambitious government policies, increasing foreign investment, and a growing domestic demand for clean mobility, the EV sector is experiencing exponential growth. However, the efficient and high-quality production of intricate EV components hinges on advanced manufacturing technologies, and at the forefront of this revolution are CNC drilling machines.
This comprehensive article delves into the crucial role of Thailand CNC Drilling Machine Market burgeoning EV component manufacturing landscape. We will explore the specific applications of these machines, the key market trends, the demands of EV component production, and the factors driving the adoption of advanced drilling solutions in the Thai market.
The Electric Vehicle Revolution in Thailand: A Manufacturing Powerhouse Emerges
Thailand's commitment to sustainable transportation has spurred significant investment and development in the EV industry. The government's "30@30" policy aims for 30% of all vehicles produced in Thailand to be electric by 2030, attracting major global EV manufacturers and component suppliers to establish production facilities in the country.
This surge in EV manufacturing necessitates a robust and sophisticated supply chain for critical components such as:
- Battery Packs: Housing cells, modules, and intricate cooling systems.
- Electric Motors: Including stators, rotors, and motor housings requiring precise assembly.
- Power Electronics: Inverters, converters, and onboard chargers demanding accurate mounting and cooling solutions.
- Chassis and Structural Components: Lightweight yet strong frames and body parts requiring precise drilling for assembly.
- Thermal Management Systems: Components for battery and motor cooling, involving complex fluid pathways.
The intricate designs and stringent quality standards of these EV components demand manufacturing processes that offer exceptional precision, repeatability, and efficiency – qualities that CNC drilling machines inherently provide.
The Indispensable Role of CNC Drilling Machines in EV Component Manufacturing
CNC (Computer Numerical Control) drilling machines are automated machine tools that perform drilling operations with high accuracy and speed based on pre-programmed instructions. Their versatility and precision make them indispensable for various stages of EV component manufacturing in Thailand:
- Battery Pack Manufacturing:
- Cooling Plate Drilling: Battery packs require efficient thermal management. CNC drilling machines create precise holes for coolant channels in battery cooling plates, ensuring optimal temperature regulation and battery lifespan. Accuracy is paramount to prevent leaks and ensure uniform cooling.
- Module Housing Drilling: Drilling mounting holes for battery cells and modules within their housings requires high precision to ensure secure and stable assembly.
- Busbar Drilling: Connecting battery cells and modules often involves busbars that need precisely drilled holes for bolting or welding, ensuring reliable electrical conductivity.
- Electric Motor Manufacturing:
- Stator Housing Drilling: Motor housings require accurately drilled holes for mounting bearings, sensors, and cooling systems. The concentricity and alignment of these holes are critical for motor performance and longevity.
- Rotor Component Drilling: Depending on the motor design, CNC drilling might be used for balancing holes or for securing specific rotor components.
- End Shield Drilling: End shields that enclose the motor require precise drilling for bearing seats and mounting features.
- Power Electronics Manufacturing:
- Heat Sink Drilling: Power electronic components generate significant heat. CNC drilling machines create precise mounting holes for heat sinks, ensuring efficient thermal dissipation and component reliability.
- Circuit Board Mounting: While not direct drilling of the board itself, CNC drilling is crucial for creating accurate mounting holes on enclosures and supporting structures for power electronic assemblies.
- Chassis and Structural Component Manufacturing:
- Light weighting Initiatives: EVs prioritize light weighting for increased efficiency. CNC drilling can create precise holes in aluminum or composite chassis components for joining using rivets or bolts, maintaining structural integrity while minimizing weight.
- Suspension and Steering System Drilling: Accurate drilling is essential for mounting points in suspension arms, steering knuckles, and other critical chassis components, directly impacting vehicle safety and handling.
- Thermal Management System Manufacturing:
- Coolant Line Drilling: Creating precise holes and ports in housings and manifolds for coolant flow is crucial for the thermal management of batteries and motors.
- Connector Drilling: Drilling accurate holes for the integration of various thermal management system connectors ensures leak-proof and efficient operation.
Key Trends Driving the Adoption of Advanced CNC Drilling Machines in Thailand's EV Sector:
Several key trends are fueling the demand for sophisticated CNC drilling solutions within Thailand's EV component manufacturing market:
- Increasing Production Volumes: As EV adoption accelerates, component manufacturers need to scale up production significantly. CNC machines offer the speed and automation necessary to meet these high-volume demands.
- Stringent Quality Standards: The safety and performance of EVs are paramount. CNC drilling machines provide the precision and repeatability required to meet the tight tolerances and quality standards of EV components.
- Demand for Lightweight Materials: The use of lightweight materials like aluminum alloys and composites in EVs necessitates drilling solutions that can handle these materials efficiently and without compromising their structural integrity. Advanced CNC machines offer specialized drilling cycles and tooling for such materials.
- Growing Complexity of Components: EV components are becoming increasingly complex, requiring intricate drilling patterns and multi-axis machining capabilities. Advanced CNC drilling centers with multiple axes and sophisticated control systems are essential to manufacture these complex parts.
- Integration of Automation: To enhance efficiency and reduce labor costs, EV component manufacturers are increasingly integrating CNC drilling machines with robotic loading/unloading systems and automated material handling solutions.
- Focus on Sustainability: Modern CNC machines are becoming more energy-efficient, aligning with the sustainability goals of the EV industry. Features like optimized cutting parameters and reduced coolant consumption contribute to a greener manufacturing process.
Challenges and Opportunities in the Thailand CNC Drilling Machine Market for EV Manufacturing:
While the outlook for CNC drilling machines in Thailand's EV sector is promising, there are also challenges and opportunities to consider:
Challenges:
- Skilled Workforce Development: Operating and maintaining advanced CNC machines requires a skilled workforce. Thailand needs to invest in training programs to develop the necessary expertise.
- Initial Investment Costs: High-end CNC drilling machines represent a significant capital investment, which can be a barrier for smaller component manufacturers.
- Integration with Existing Systems: Integrating new CNC machines with existing manufacturing systems and software can present technical challenges.
Opportunities:
- Meeting the Growing Demand: The rapid expansion of EV manufacturing in Thailand presents a significant market opportunity for CNC machine tool suppliers.
- Providing Turnkey Solutions: Offering comprehensive solutions that include the CNC machine, tooling, automation integration, and training can be a competitive advantage.
- Focusing on Specific EV Component Needs: Tailoring CNC drilling solutions to the specific requirements of battery, motor, and chassis component manufacturing can address niche market demands.
- Leveraging Government Incentives: The Thai government's support for the EV industry may also extend to incentives for adopting advanced manufacturing technologies.
The Future of CNC Drilling in Thailand's EV Ecosystem:
The future of CNC drilling machines in Thailand's EV component manufacturing sector is inextricably linked to the continued growth and sophistication of the industry. We can expect to see:
- Increased Adoption of High-Speed and High-Precision Machines: To meet the demands of mass production and stringent quality standards.
- Greater Integration of Multi-Axis Machining Centers: For producing complex geometries in a single setup, reducing cycle times and improving accuracy.
- Enhanced Connectivity and Data Analytics: CNC machines integrated with IoT (Internet of Things) for real-time monitoring, predictive maintenance, and process optimization.
- Development of Specialized Tooling and Cutting Strategies: Optimized for the specific materials used in EV components, such as aluminum, composites, and high-strength steels.
Conclusion
CNC drilling machines are not merely supporting actors in Thailand's EV revolution; they are critical enablers of efficient, precise, and high-quality component manufacturing. As the Thai EV market continues its rapid ascent, the demand for advanced CNC drilling solutions will only intensify. By embracing cutting-edge technology, investing in skilled labor, and focusing on the specific needs of EV component production, Thailand can solidify its position as a leading EV manufacturing hub, with CNC drilling machines playing a pivotal role in driving this success. The precision and efficiency offered by these machines will be instrumental in ensuring that Thailand-made EV components meet the rigorous demands of the global electric vehicle market.
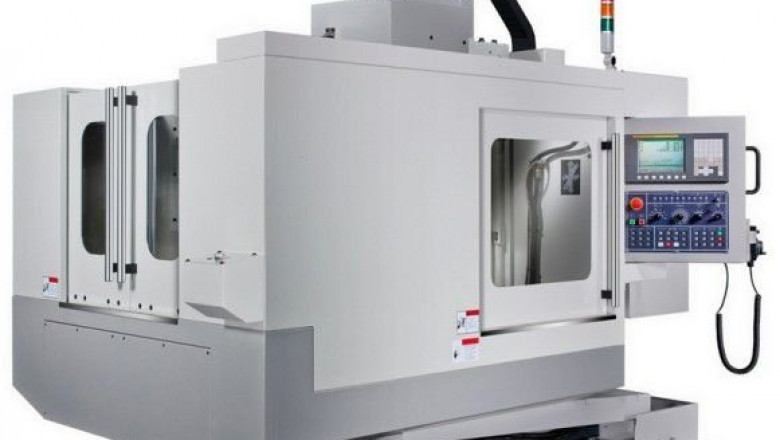
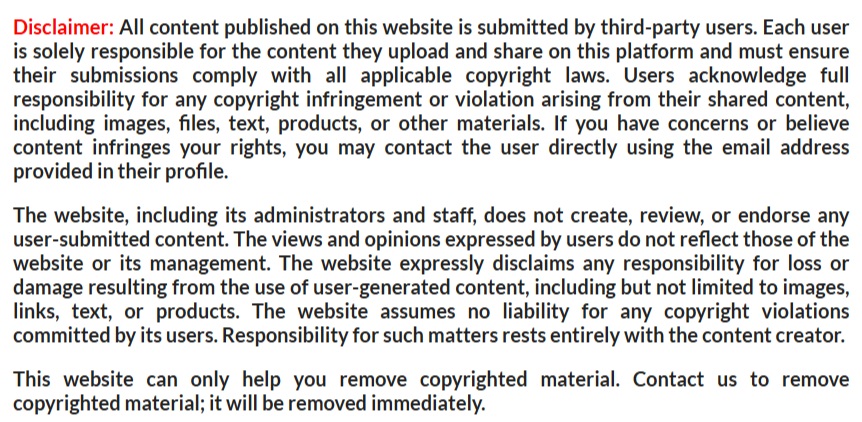
Comments
0 comment