views
Introduction:
The Ceramic Machinery Market has witnessed substantial growth in recent years, driven by innovations that improve manufacturing processes, product quality, and energy efficiency. One of the most notable advancements in the industry is in glazing technology.
This article will explore the evolution of glazing technology in ceramic machinery, highlighting key innovations and trends that have reshaped this aspect of ceramic production. We will also examine the impact of these advancements on the overall ceramic machinery market and future developments.
Overview of the Ceramic Machinery Market
The ceramic machinery market encompasses a wide range of equipment and technologies used in the production of ceramic products. These products include tiles, sanitary ware, porcelain, pottery, and industrial ceramics. The machinery required for the production process ranges from presses, extruders, and molding machines to dryers, kilns, and glaze application systems.
The global market for ceramic machinery is projected to experience significant growth, driven by increased demand for ceramic products across various sectors, such as construction, interior design, and industrial applications. The focus on sustainability, energy efficiency, and product quality is influencing the evolution of technologies used in ceramic manufacturing, including the crucial process of glazing.
Understanding Glazing in Ceramic Production
Glazing is the process of applying a thin, glass-like coating to a ceramic product, usually by spraying, dipping, or rolling the glaze onto the surface of the item. The primary purpose of glazing is to enhance the aesthetic appearance, provide a smooth surface, and add protection against wear, water, and stains. Additionally, glazing can affect the final product's texture, color, and sheen.
The glaze is applied to the ceramic body after it has been shaped and partially fired (bisque-fired). After glazing, the product undergoes a final firing process in the kiln to melt the glaze, fusing it with the ceramic surface.
The evolution of glazing technology has been essential to improving product quality, enhancing decorative options, and reducing environmental impact. Over time, ceramic manufacturers have developed more sophisticated machinery to apply glazes consistently and efficiently, allowing for better control over glaze thickness, color uniformity, and surface finish.
The Evolution of Glazing Technology in Ceramic Machinery
The advancement of glazing technology in ceramic machinery can be traced through several key stages, each marked by technological breakthroughs that have improved efficiency, precision, and sustainability.
1. Manual Glazing Techniques: Early Beginnings
In the early days of ceramic manufacturing, glazing was a manual process that required skilled artisans to apply glazes by hand using brushes, sponges, or dipping techniques. While this allowed for detailed, intricate designs, it was a time-consuming process that resulted in inconsistent glaze coverage, leading to variations in quality.
Manual glazing also posed challenges in terms of waste, as excess glaze had to be discarded, and the overall process was labor-intensive. Moreover, the lack of automation meant that only small-scale production could be achieved, limiting the scalability of the industry.
2. Spray Glazing Systems: A Turning Point
The introduction of spray glazing marked a significant milestone in the evolution of glazing technology. Spray glazing systems use compressed air or airless spraying techniques to apply a fine mist of glaze onto the ceramic surface. This technology allowed for more uniform coverage, faster application, and better control over glaze thickness.
Spray glazing systems became widely adopted in ceramic tile production, where the need for large-scale manufacturing and consistent product quality was paramount. The use of spray systems also reduced waste, as excess glaze could be recycled and reused. These systems were particularly advantageous for tile manufacturers, where large volumes of products had to be glazed quickly while maintaining quality standards.
3. Roller and Roller-Press Glazing Systems
As the demand for efficiency and precision increased, roller and roller-press glazing systems emerged as a more effective alternative to spray glazing. These systems use rollers to evenly distribute the glaze over the surface of the ceramic product as it passes through a series of rollers. The process is highly automated, resulting in precise control over glaze thickness and consistency.
Roller and roller-press glazing systems are commonly used in the production of ceramic tiles and other flat ceramic products. The key advantage of this method is that it allows for the continuous application of glaze to large numbers of products, making it ideal for high-volume production. These systems can also apply multiple layers of glaze in one pass, enabling manufacturers to create products with more complex surface finishes and textures.
4. Inkjet Printing: Digital Glazing Revolution
One of the most groundbreaking advancements in glazing technology in recent years is the use of inkjet printing for ceramic surface decoration. Inkjet printers can apply glazes or decorative patterns directly onto the surface of the ceramic product using digital technology. This approach offers several benefits over traditional glazing methods.
Precision and Customization
Inkjet printing enables precise control over glaze application, allowing for intricate and highly detailed designs. This technology is particularly valuable for creating custom designs and patterns on ceramic surfaces, offering a level of flexibility that was previously impossible with traditional methods. Manufacturers can produce unique, bespoke ceramic pieces in small batches or even single units without the need for expensive molds or templates.
Reduced Waste
Unlike traditional glazing methods that often result in excess glaze, inkjet printing uses only the required amount of ink or glaze for each print, significantly reducing waste. This is particularly important for sustainability and cost-efficiency, as it minimizes material usage and helps manufacturers meet environmental standards.
Faster Production
Inkjet printing also speeds up the glazing process. Since the glaze is applied directly onto the surface, the time-consuming steps of dipping, spraying, or rolling are eliminated. This means that manufacturers can achieve faster turnaround times, which is essential for meeting market demands and reducing production lead times.
Inkjet printing technology has also paved the way for high-definition ceramic designs, including photographic-quality images, textures, and gradients, allowing manufacturers to create visually stunning and highly customizable ceramic products.
5. Advanced Glaze Application Robots
As automation in the ceramic industry continues to evolve, glaze application robots are playing an increasingly important role in improving efficiency and precision. These robots are capable of applying glaze uniformly and consistently across a wide range of ceramic products, from tiles to sanitary ware, without the need for human intervention.
These robots can be programmed to follow specific glaze application patterns, ensuring that the coating is applied precisely according to the desired thickness and texture. Robots also enhance production speed by eliminating downtime associated with manual application, making them ideal for high-volume, large-scale ceramic manufacturing operations.
Additionally, robotic systems can be integrated with real-time monitoring technology to ensure quality control during the glazing process. Sensors can track the glaze thickness, temperature, and consistency, providing valuable data that can be used to optimize the process and maintain high standards of quality.
6. Sustainability in Glazing Technology
In response to increasing environmental concerns and regulatory pressures, the ceramic industry is adopting more sustainable glazing technologies. These innovations aim to reduce energy consumption, minimize waste, and lower the carbon footprint of the glazing process.
Water-Based Glazes
In the past, many glazes contained harmful chemicals, including solvents and other volatile organic compounds (VOCs). Today, manufacturers are increasingly using water-based glazes, which are less toxic and more environmentally friendly. Water-based glazes not only reduce harmful emissions but also improve the safety of workers involved in the glazing process.
Low-Temperature Firing
Another advancement in sustainable glazing technology is the development of low-temperature firing methods. Traditional ceramic glazing requires firing at very high temperatures, which consumes significant amounts of energy. However, with new innovations in glaze chemistry, it is now possible to achieve high-quality results with lower firing temperatures. This reduces energy consumption and lowers emissions associated with the firing process.
Recyclable Glazes
Manufacturers are also exploring the use of recyclable glazes in the production process. These glazes can be reused or repurposed, reducing waste and contributing to a more circular economy. This trend is gaining traction in the industry as sustainability becomes an increasingly important factor in consumer purchasing decisions.
Impact of Glazing Technology on the Ceramic Machinery Market
The evolution of glazing technology has had a significant impact on the ceramic machinery market as a whole. Advancements in glaze application systems have led to increased demand for more sophisticated machinery that can handle the complexities of modern ceramic production.
As manufacturers seek greater automation, precision, and efficiency in their operations, the demand for advanced glazing machines, including inkjet printers, robotic systems, and automated glazing lines, is rising. These machines not only help manufacturers meet production demands but also enable them to produce higher-quality products with a wide range of aesthetic and functional characteristics.
Moreover, as sustainability becomes a key focus in the ceramic industry, there is an increasing demand for eco-friendly glazing technologies that minimize environmental impact while maintaining high product quality. Manufacturers who adopt these sustainable practices are likely to gain a competitive edge in the market.
Conclusion
The evolution of glazing technology in the ceramic machinery market has been a transformative journey, from manual methods to the integration of advanced automation and digital technologies. The rise of inkjet printing, robotic glaze application, and sustainable glazing solutions has dramatically improved the quality, efficiency, and sustainability of the glazing process.
As the ceramic industry continues to innovate and evolve, we can expect further advancements in glazing technology that will enable manufacturers to produce even more diverse, high-quality ceramic products with reduced environmental impact. The future of glazing in ceramic production is undoubtedly bright, and as technology continues to progress, the machinery used in this process will play an increasingly important role in shaping the industry’s future.
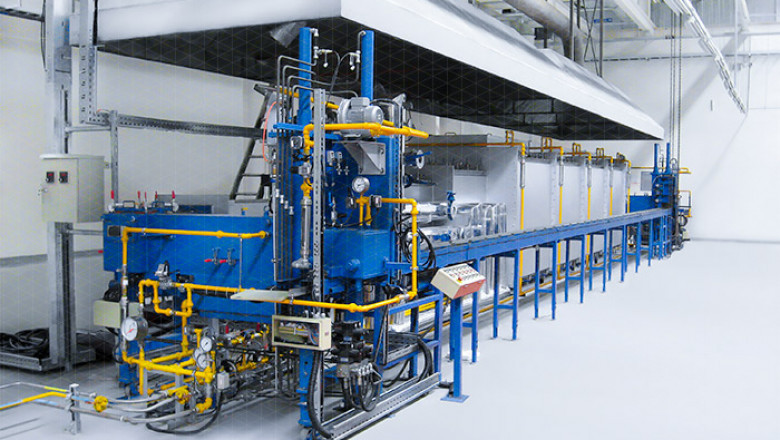

Comments
0 comment