views
The burn-off oven market, essential for industrial surface treatment and parts reclamation, faces several significant hindrances that impede growth and innovation. Burn-off ovens remove paints, powder coatings, adhesives, and organic residues from metal components, playing a critical role in automotive remanufacturing, aerospace maintenance, foundries, and heavy equipment repair. Despite their importance, operators and manufacturers grapple with a range of challenges—from high operating costs and regulatory pressures to technical limitations and workforce shortages. Understanding these hindrances is crucial for stakeholders seeking to optimize operations and drive sustained market expansion.
1. High Energy Consumption and Volatile Fuel Costs
Burn-off ovens typically operate at temperatures between 400°C and 600°C for extended cycles, consuming large amounts of natural gas or propane. Rising and unpredictable energy prices translate directly into inflated operating expenses. While energy-efficient technologies—such as improved insulation, recuperative burners, and heat-recovery systems—can reduce fuel use by up to 30%, the substantial capital investment required often deters smaller shops. Consequently, many facilities continue to rely on older, less efficient ovens, perpetuating high energy costs and undermining competitiveness.
2. Stringent Emissions Regulations
Air-quality standards are tightening globally, with authorities imposing lower thresholds on volatile organic compounds (VOCs), hazardous air pollutants (HAPs), and nitrogen oxides (NOₓ) emitted during burn-off processes. Conventional ovens equipped only with basic afterburners struggle to comply, forcing users to install costly emissions-control equipment—such as regenerative thermal oxidizers, catalytic converters, or scrubbers. These systems add substantial capital and maintenance expenses and often increase energy demand, creating a regulatory-cost spiral that slows new installations and retrofits alike.
3. Maintenance Complexity and Downtime
Burn-off ovens require regular upkeep to maintain performance and safety. Critical components—refractory linings, burner assemblies, fans, and ductwork—degrade over time due to thermal cycling and particulate abrasion. Scheduled maintenance often necessitates partial or full oven shutdowns, leading to production backlogs and lost revenue. Unplanned breakdowns exacerbate the problem, with emergency repairs incurring premium labor and expedited parts costs. The lack of predictive-maintenance tools in many facilities means operators frequently rely on time-based servicing, resulting in either premature part replacement or unexpected failures.
4. Safety and Operator Health Risks
Operating at high temperatures and handling combustible gases, burn-off ovens present inherent safety hazards. Workers face risks of burns, exposure to toxic off-gases, and mechanical injuries during loading and unloading. Inadequate ventilation and gas-detection systems can lead to dangerous fume buildup, while manual handling of heavy fixtures strains personnel. Compliance with workplace safety regulations demands investments in protective equipment, training programs, and automated load-handling systems, all of which add to capital and operating expenses—particularly burdensome for small and mid-sized enterprises.
5. Skill Shortages and Training Gaps
The effective operation and maintenance of modern burn-off ovens demand specialized skills in combustion tuning, refractory renewal, control-system programming, and safety-system management. Yet the industry faces a growing shortage of experienced technicians as veteran personnel retire and fewer young workers enter industrial trades. This skills gap leads to longer downtimes, improper maintenance, and heightened safety risks. Developing comprehensive training programs and attractive career pathways is essential but requires time and funding that many firms cannot readily allocate.
6. Space Limitations and Facility Integration
Large, stationary burn-off ovens often require substantial shop floor space, dedicated foundations, and complex utility connections (gas, electrical, exhaust). Retrofitting these ovens into existing facilities can disrupt workflows and demand costly structural modifications. Modular or skid-mounted units offer greater flexibility but still need careful planning for material handling, power supply, and exhaust routing. Space-constrained urban or legacy plants may find it challenging to accommodate modern oven designs, slowing equipment upgrades and modernization efforts.
7. Supply Chain Disruptions
Global supply-chain volatility has impacted the availability and cost of critical oven components—precision burners, refractory materials, control panels, and insulation. Extended lead times, raw-material shortages, and shipping delays force manufacturers to maintain expanded inventories or qualify multiple suppliers, driving up working capital requirements. End users experience delayed equipment deliveries and prolonged downtime, eroding confidence in supplier reliability and hindering adoption of new technologies.
8. Competition from Alternative Cleaning Technologies
Emerging non-combustion cleaning methods—such as dry-ice blasting, ultrasonic cleaning, and chemical stripping—offer residue removal without high-temperature cycles or combustion emissions. While these alternatives may involve secondary hazards (abrasive media, chemical disposals) and often higher per-cycle costs, they attract operators seeking lower energy usage and simpler emissions compliance. The growing interest in hybrid cleaning lines, combining low-temperature ovens with abrasive or chemical stages, poses a competitive threat to traditional burn-off ovens in specialized applications.
9. Capital Budget Constraints
Many end users, especially in the small and medium-sized enterprise segment, operate under tight capital budgets. High upfront costs for advanced ovens—equipped with energy recovery, emissions controls, and automation—can be prohibitive. Financing options such as leasing or performance-based service contracts exist but are not universally accessible. Without clear internal cases demonstrating rapid payback through fuel savings, maintenance reduction, and increased throughput, decision-makers often defer upgrades, perpetuating reliance on outdated equipment.
10. Customization Complexity
Different industries and applications demand tailored oven configurations—batch versus continuous designs, inert-gas atmospheres for non-oxidizing processes, specialized load fixtures for complex part geometries, and varying cycle times. This customization increases design and manufacturing complexity, extends lead times, and raises costs. Standardized, off-the-shelf solutions may not meet specific user requirements, while fully custom ovens can strain OEM resources and complicate after-sales support.
Conclusion
The burn-off oven market confronts a constellation of hindrances—from high energy and compliance costs to maintenance complexity, safety risks, skill shortages, and supply-chain fragilities. Moreover, competition from alternative cleaning technologies and budgetary constraints further challenge growth. Addressing these barriers requires holistic strategies: investing in energy-efficient designs, modular and digitally enabled solutions, workforce development, and flexible financing models. By tackling these pain points head-on, equipment suppliers and industrial operators can enhance process efficiency, meet regulatory demands, and secure long-term market viability.
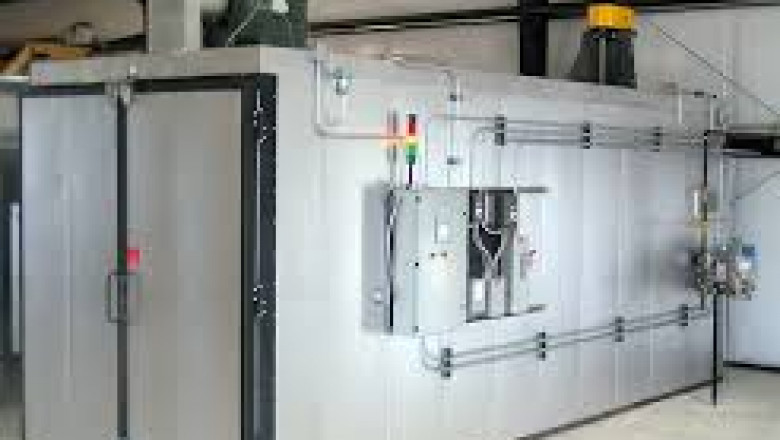
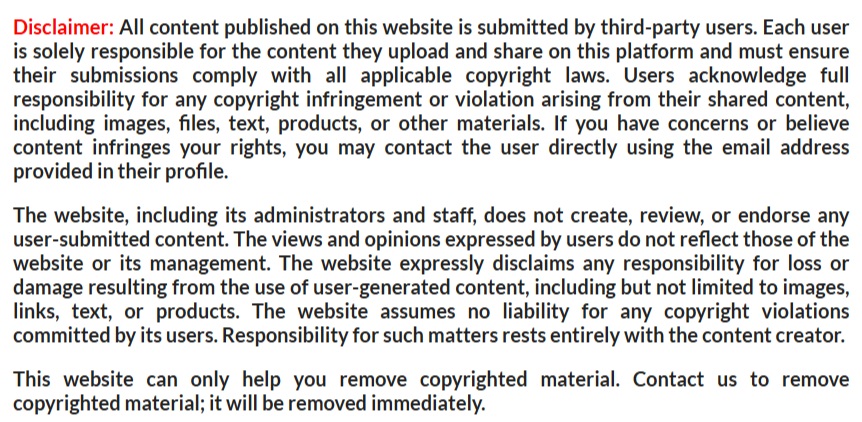
Comments
0 comment