views
The automotive turbocharger market is driven by an intricate supply chain that involves raw material suppliers, component manufacturers, assembly plants, and distribution networks. As turbochargers continue to play a vital role in enhancing fuel efficiency and reducing emissions, supply chain efficiency is crucial for meeting global demand. This article explores the key aspects of the turbocharger supply chain, recent developments, and the impact of market dynamics on suppliers and manufacturers.
Supply Chain Analysis
1. Raw Material Sourcing and Procurement
Turbochargers require high-quality materials such as stainless steel, aluminum alloys, and heat-resistant composites. The procurement of these raw materials is a critical step in the supply chain, with global suppliers playing a significant role in ensuring cost efficiency and product durability. Fluctuations in raw material prices, particularly for metals and alloys, can impact overall production costs.
2. Component Manufacturing and Supplier Network
Key components of a turbocharger include the turbine, compressor, bearings, and actuators. These components are manufactured by specialized suppliers who ensure precision engineering to optimize turbocharger performance. The global supplier network includes companies from regions such as North America, Europe, and Asia-Pacific, with China and Japan being major hubs for component production.
3. Turbocharger Assembly and Quality Control
Turbocharger assembly involves integrating individual components to create high-performance systems. Leading manufacturers employ automated production lines and stringent quality control measures to enhance product reliability. The adoption of Industry 4.0 technologies, such as IoT-enabled monitoring and predictive maintenance, is improving manufacturing efficiency and reducing production downtime.
4. Distribution and Logistics
Turbochargers are distributed to automakers, aftermarket retailers, and service centers worldwide. Efficient logistics and inventory management are crucial to ensuring timely deliveries and minimizing supply chain disruptions. Companies are investing in digital supply chain solutions to enhance visibility and reduce lead times.
5. Aftermarket Supply Chain and Service Networks
The aftermarket segment for turbochargers plays a significant role in the supply chain. As turbochargers require periodic maintenance and replacements, an extensive service network is necessary to meet customer demands. Distributors and service providers ensure the availability of replacement parts, boosting the aftermarket business.
Key Developments in the Automotive Turbocharger Market
1. Advancements in Electrically Assisted Turbochargers
Major turbocharger manufacturers are investing in electrically assisted turbochargers (e-turbos) to improve engine response and reduce emissions. These advanced systems integrate electric motors to eliminate turbo lag and enhance overall efficiency, making them ideal for hybrid and mild-hybrid vehicles.
2. Strategic Partnerships and Mergers
The turbocharger market is witnessing increased collaboration between automakers and turbocharger suppliers. Companies are forming strategic alliances to enhance R&D capabilities, optimize production costs, and expand their market presence. Mergers and acquisitions are also driving consolidation within the industry, strengthening the supply chain.
3. Integration of 3D Printing in Turbocharger Manufacturing
The adoption of additive manufacturing (3D printing) is revolutionizing turbocharger production. Manufacturers are leveraging 3D printing technology to create complex turbine blade designs, reduce material waste, and enhance production efficiency. This innovation is expected to streamline the supply chain and lower manufacturing costs.
4. Expansion of Turbocharger Production Facilities
To meet the growing demand for turbocharged vehicles, companies are expanding their production facilities in key automotive markets. Asia-Pacific, particularly China and India, has emerged as a major hub for turbocharger production due to favorable government policies, lower labor costs, and increasing vehicle production.
5. Impact of Semiconductor Shortages and Supply Chain Disruptions
The global semiconductor shortage has impacted the production of modern turbochargers, particularly those with electronic actuators and variable geometry systems. Supply chain disruptions caused by geopolitical tensions, raw material shortages, and transportation bottlenecks have also affected turbocharger availability, prompting manufacturers to explore alternative sourcing strategies.
Final Thoughts
The automotive turbocharger market relies on a robust and efficient supply chain that integrates raw material sourcing, component manufacturing, assembly, and distribution. Recent advancements, including electrified turbochargers, 3D printing, and strategic partnerships, are shaping the future of the industry. However, challenges such as supply chain disruptions and material shortages require adaptive strategies to ensure sustained growth. Companies that invest in innovation, digital supply chain management, and regional production expansion will gain a competitive advantage in this evolving market.
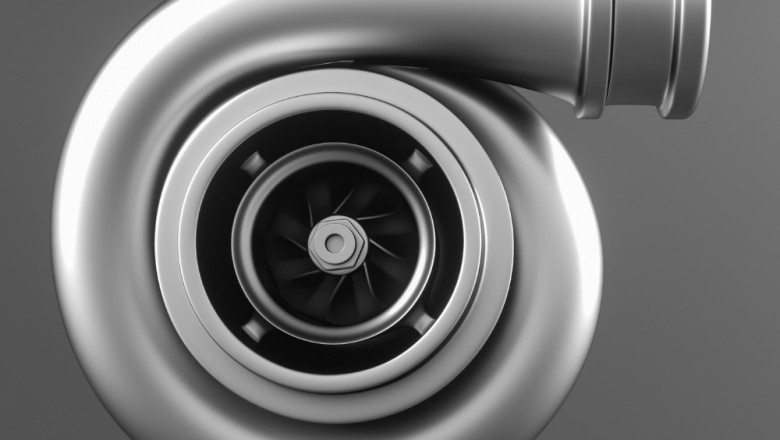

Comments
0 comment