views
The automotive foams market plays a vital role in the development of vehicles, contributing to comfort, safety, sound insulation, and energy efficiency. However, as the industry evolves with the rise of electric vehicles (EVs), sustainability concerns, and increasing consumer expectations, manufacturers face several challenges in meeting the demands of the market. This article examines the key challenges faced by manufacturers in the automotive foams market and presents potential solutions to navigate these issues effectively.
Key Challenges Facing Manufacturers
- Stringent Environmental Regulations
Environmental regulations around the world are becoming more stringent, with governments imposing stricter standards on emissions and material sustainability. Manufacturers of automotive foams must ensure that their products comply with these regulations, which often include the use of eco-friendly materials and the reduction of harmful chemicals in production.
In the context of electric vehicles (EVs), the push for reducing the environmental impact of materials used in vehicles, including foams, is especially significant. This presents a challenge for foam manufacturers to balance performance, safety, and environmental considerations.
Solution: Adoption of Sustainable Materials
To address the growing regulatory pressures, manufacturers can focus on the development of sustainable foams made from renewable and recyclable materials. Bio-based foams derived from plant-based sources, such as soy or castor oil, can serve as a sustainable alternative to petroleum-based materials. Additionally, foam manufacturers should explore the use of recycled foam materials and develop processes that allow for easier recycling of used foams from vehicles.
The implementation of lifecycle assessments (LCAs) to track the environmental impact of foam materials from production to end-of-life disposal can also help manufacturers meet regulatory requirements and enhance their environmental credentials.
- Material Performance and Durability
Automotive foams must meet a variety of performance criteria, including impact resistance, durability, comfort, and temperature stability. As consumer preferences evolve, particularly with the increasing demand for electric vehicles, there is a need for foams that not only offer traditional benefits such as cushioning and noise reduction but also provide enhanced thermal management and crash protection.
Foams need to maintain their performance across a wide range of temperatures and driving conditions. This poses a challenge for manufacturers, as ensuring consistent performance while meeting weight, safety, and comfort requirements can be difficult.
Solution: Advanced Material Technologies and Testing
Manufacturers can address these performance challenges by investing in the development of advanced foam materials that offer improved properties such as greater resistance to heat, better durability, and superior energy absorption. The use of multi-layered or composite foam structures can improve thermal management and crash protection, particularly for electric vehicle batteries.
Moreover, manufacturers should implement rigorous testing protocols to evaluate the performance of foams in various real-world conditions, including extreme temperatures, vibrations, and long-term wear. This will help ensure that the foams meet the necessary durability and performance standards over the lifespan of the vehicle.
- Cost Pressures and Price Sensitivity
Cost is always a significant factor in the automotive industry, with manufacturers under constant pressure to reduce production costs while maintaining quality. The growing demand for lightweight materials and advanced foam technologies, such as high-density and memory foams, often leads to higher production costs. For manufacturers, balancing the need for high-performance materials with cost efficiency can be a difficult task.
Additionally, fluctuations in the prices of raw materials, such as petroleum-based products and chemical additives, can lead to price volatility, affecting the overall cost of production.
Solution: Process Optimization and Supply Chain Management
To address cost pressures, manufacturers can focus on optimizing production processes to reduce waste and improve efficiency. Implementing lean manufacturing techniques, such as reducing excess inventory and enhancing supply chain management, can help minimize operational costs.
Collaborating with suppliers to secure long-term contracts for key raw materials or exploring alternative sources of materials may help mitigate price volatility. Additionally, the adoption of automation and digital technologies in manufacturing can improve efficiency and reduce labor costs, ultimately contributing to cost savings.
- Consumer Demand for Customization and Premium Features
Consumer expectations are evolving, with a growing demand for personalized and premium features in vehicles. In the automotive foams market, this translates to the need for foams that offer not only functional benefits such as comfort and safety but also aesthetics and customization. Automotive manufacturers are increasingly integrating foams with features like memory foam, ergonomic designs, and advanced acoustics to enhance the driving experience.
This trend toward luxury and customization presents a challenge for foam manufacturers, as they must develop a wide range of products that can cater to various consumer preferences across different vehicle segments.
Solution: Flexible Manufacturing and Product Innovation
To meet consumer demand for customization, manufacturers should adopt flexible manufacturing techniques that allow for the efficient production of a wide variety of foam products in different shapes, densities, and materials. By offering a broader range of foam options, manufacturers can cater to the needs of both mass-market vehicles and premium models.
Innovation in foam technologies, such as integrating foams with smart materials that respond to temperature or pressure changes, can also help manufacturers stay ahead of consumer preferences for luxury and personalized vehicle interiors.
- Supply Chain and Raw Material Shortages
Like many industries, the automotive foams market is facing disruptions in the supply chain, particularly in the availability of raw materials and transportation. The COVID-19 pandemic, geopolitical tensions, and trade disruptions have made it difficult for manufacturers to secure a consistent supply of critical materials such as polyurethane, melamine, and other chemicals used in foam production. Shortages in these raw materials can result in delayed production timelines and increased costs.
Solution: Diversification of Supply Sources
To mitigate the risks associated with supply chain disruptions, manufacturers can diversify their supply sources and build more resilient supply chains. This may include sourcing materials from different regions or developing relationships with multiple suppliers to reduce dependency on a single source.
Additionally, manufacturers can consider investing in local supply chains, reducing reliance on global networks, and fostering closer relationships with suppliers to ensure a more stable and reliable flow of materials.
Final Thoughts
The automotive foams market is at the crossroads of significant challenges and opportunities. Manufacturers are faced with growing pressure to meet stringent environmental regulations, adapt to shifting consumer preferences, and navigate economic challenges while delivering high-quality products. By embracing sustainability, investing in advanced materials, optimizing production processes, and innovating to meet the demands of an increasingly diverse market, automotive foam manufacturers can position themselves for success in the rapidly evolving automotive industry.
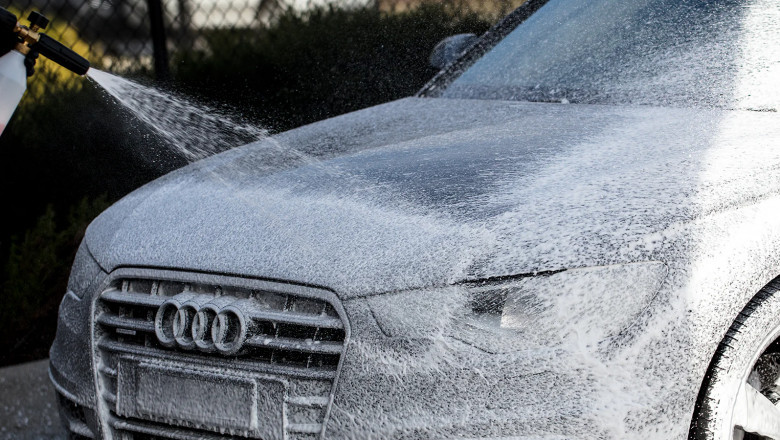

Comments
0 comment