views
EPC contracts are crucial in the construction industry. They outline a comprehensive agreement between a project owner and a contractor. Under this arrangement, the contractor takes on the responsibility for engineering, procurement, and construction. This integrated approach simplifies project management and coordination. It streamlines communication and reduces delays, ultimately leading to enhanced project efficiency.
Understanding EPC contracts is vital for both owners and contractors. The clarity these contracts provide can minimize disputes and misunderstandings. It allows for clear expectations from the outset. Additionally, this contract type can lead to improved timelines and budgets. By engaging in this structure, stakeholders can achieve a more cohesive project execution.
What is an EPC Contract?
An EPC contract represents a specific type of agreement in the construction industry. It involves three main phases: engineering, procurement, and construction. The contractor manages all aspects of the project, from initial design to final delivery. This includes sourcing materials, hiring subcontractors, and overseeing construction work.
This contract model is beneficial for owners seeking a single point of contact. It reduces the complexity of dealing with multiple contracts. Furthermore, the contractor assumes responsibility for project delivery. Effective planning and execution are essential for success. In addition, construction estimating services play a crucial role in determining project costs upfront, helping to ensure the project remains within budget.
Key Components of EPC Contracts
Several key elements define EPC contracts. The agreement typically includes project scope, timelines, and payment terms. A detailed description of the work to be performed is essential. It ensures all parties have a clear understanding of expectations. Milestones and deadlines should also be clearly outlined.
Payment structures are another critical component. These agreements often involve fixed-price contracts. This arrangement helps mitigate financial risks for the owner. Additionally, performance guarantees are common in EPC contracts. These guarantees ensure that the contractor meets specific performance criteria throughout the project lifecycle.
Advantages of EPC Contracts for Projects
EPC contracts offer numerous benefits. One of the most significant advantages is a streamlined process. Since one entity handles engineering, procurement, and construction, communication improves. This reduces the potential for misunderstandings and delays. The cohesive approach also fosters better collaboration among teams.
Another benefit is risk management. The contractor assumes responsibility for delivering the project on time and within budget. This structure shifts some risk away from the project owner. As a result, owners can focus on their core business while trusting the contractor to deliver a successful project. Overall, EPC contracts enhance efficiency and accountability.
Disadvantages of EPC Contracts
While EPC contracts have many advantages, they also present challenges. One potential downside is the reliance on a single contractor. If the contractor underperforms, the entire project may suffer. This can lead to delays and increased costs. Owners must carefully vet potential contractors to mitigate this risk.
Another concern is the limited flexibility in project changes. Once the contract is signed, altering the project scope can be complicated. This rigidity may lead to additional costs or delays if changes are necessary. Owners should weigh these disadvantages against the benefits before choosing this contracting method.
Roles and Responsibilities in EPC Contracts
Understanding roles and responsibilities is vital in EPC contracts. The contractor assumes the primary responsibility for project execution. This includes managing all phases, from design to construction. The owner’s role is to provide clear project objectives and timely approvals.
Additionally, subcontractors may be engaged by the contractor to perform specific tasks. Each party must understand its responsibilities to avoid conflicts. Effective communication is essential throughout the project. Regular updates and meetings can help ensure everyone remains aligned with project goals.
The EPC Contracting Process
The contracting process for EPC projects involves several steps. Initially, the project owner identifies the need for an EPC contractor. This includes preparing detailed project specifications and timelines. Next, the owner solicits proposals from potential contractors. Evaluating these proposals is critical to selecting the right partner.
Once a contractor is chosen, negotiations commence. This stage focuses on finalizing contract terms, including scope, pricing, and timelines. After the contract is signed, the project moves into the execution phase. Throughout this phase, continuous monitoring and communication are essential for success.
Risk Management in EPC Contracts
Effective risk management is crucial in EPC contracts. Contractors must identify potential risks early in the project. These risks can include cost overruns, delays, and resource shortages. Implementing strategies to mitigate these risks helps ensure project success.
Regular assessments throughout the project lifecycle are important. By monitoring progress, contractors can adapt to unforeseen challenges. Additionally, maintaining open communication with the project owner is vital. This collaboration fosters a proactive approach to addressing potential issues before they escalate.
EPC vs. Traditional Contracting Methods
Comparing EPC contracts to traditional methods reveals distinct differences. In traditional contracting, multiple contracts may exist for various project phases. This can lead to communication challenges and fragmented responsibility. In contrast, EPC contracts streamline the process through a single agreement.
Furthermore, EPC contracts often feature fixed pricing. This contrasts with traditional methods, which may involve variable costs. The fixed-price structure in EPC contracts provides clarity for project budgeting. Understanding these differences can help owners choose the best contracting method for their projects.
Common Challenges in EPC Contracts
EPC contracts can present unique challenges. One common issue is scope creep. Changes to project requirements can disrupt timelines and budgets. Managing expectations and maintaining clear communication helps mitigate this risk.
Another challenge is contractor performance. If the contractor fails to meet expectations, it can lead to project delays. Owners must conduct thorough due diligence when selecting contractors. Establishing performance metrics in the contract can also help hold contractors accountable.
Best Practices for Managing EPC Contracts
Effective management of EPC contracts involves several best practices. Regular communication with the contractor is essential. This ensures that all parties remain aligned on project goals and timelines. Setting up routine progress meetings can help identify potential issues early.
Additionally, utilizing project management tools can enhance oversight. These tools provide visibility into timelines, budgets, and resource allocation. Establishing clear performance metrics in the contract also fosters accountability. Implementing these best practices can lead to successful project outcomes.
Conclusion
The future of EPC contracts looks promising. As the construction industry evolves, the demand for integrated project delivery continues to grow. EPC contracts offer a streamlined approach that appeals to many project owners. Their ability to simplify communication and reduce risks is increasingly valuable.
Additionally, advancements in technology will enhance EPC contract management. Tools like Building Information Modeling (BIM) and project management software will improve efficiency. Overall, the EPC contracting model is well-positioned to play a vital role in future construction projects.
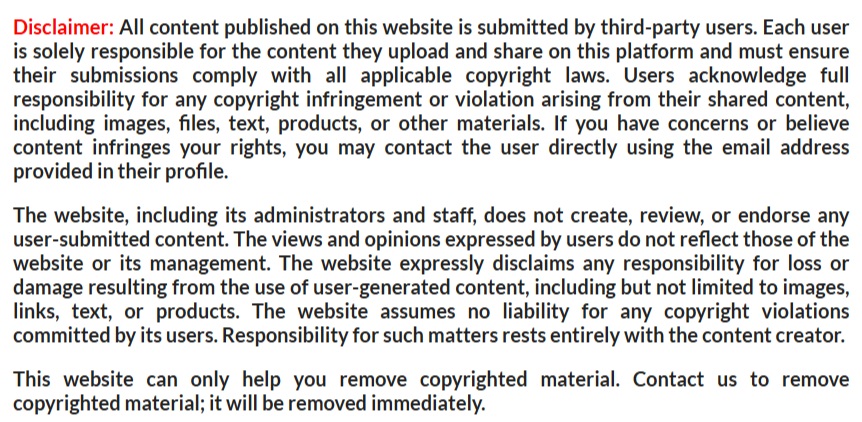