views
Trillion-Dollar Market Disruptor! Automatic OCA/OCR Lamination Equipment Ushers in the Era of Multi-Scenario Integrated Manufacturing
By 2025, the global Flexible Hybrid Electronics (FHE) market will exceed $8.7 billion, driven by emerging applications such as medical electronic skins, automotive curved displays, and military foldable devices—forcing traditional lamination equipment to evolve. Yet, industry pain points remain stark:
⚠️ 73% of manufacturers suffer daily capacity loss due to production line switching (Source: DisplaySearch 2025 Q2 Report)
⚠️ Medical/military display bubble defect rates are 3x higher than traditional screens (SGS test data)
XX Company’s fifth-generation Automatic OCA/OCR Lamination Equipment redefines industry boundaries with Multi-Scenario Dynamic Compensation Technology—
1. Breakthrough Solutions for Three High-Value Scenarios (Targeting Industry Gaps)
Scenario | Technological Revolution | Quantifiable Gains |
---|---|---|
Medical Screen Lamination | OCA Viscosity Adaptive System | Bubble defect rate ↓82% (≤0.1ppm) |
Automotive Curved Screens | Thermal Stress Compensation Engine (-40°C~85°C) | Radius compatibility ↑200% (down to R2mm) |
Military Screen Manufacturing | Anti-Shock Vibration Damping Module (MIL-STD-810H certified) | High-vibration environment yield ≥99.5% |
⚡ 2. Dynamic Precision Matrix (Shattering Traditional Limits)
Automatic OCA Lamination Equipment | Optimized for Wearables/Mobile Screens
2025 Industry Precision Benchmark Comparison
Parameter | Traditional Equipment | Our Equipment | Scenario Value |
---|---|---|---|
Lamination Accuracy | ±0.1mm | ±0.05mm | Eliminates micro-electrode breaks in medical screens |
Min. Compatible Size | 1.5 inches | 0.9 inches | Enables smart ring display mass production |
Temperature Stability | ±15°C range | -40°C~85°C | Solves Arctic automotive screen delamination |
Automatic OCR Lamination Equipment | Large-Scale Commercial Display Solutions
Parameter | Traditional Equipment | Our Equipment | Scenario Value |
---|---|---|---|
Max. Compatible Size | 85 inches | 110 inches | Covers digital advertising mega-screens |
Curved Lamination Yield | ≤94% | ≥99% | Reduces commercial display rework costs by $420/unit |
Cycle Time | 380 sec/panel | 300 sec/panel | Boosts military emergency screen output by 30% |
🌐 3. Cross-Industry Smart Hub System (Creating Synergistic Value)
"When switching production between medical ECG patch screens and military ruggedized tablets on the same line:
▪️ Self-Learning Recipe Management: Retrieves OCA viscosity parameters in 3 sec (error rate <0.01%)
▪️ Quantum-Level Pressure Sensing: Real-time lamination pressure adjustment (medical 0.2N/cm² vs. military 4.8N/cm²)
▪️ AI Waste Prediction Engine: Reduces OCA material waste by 37% (saving $180K/year per line)"
💡 Why Did Tesla’s Military Division Choose Us?
*"In the ‘Polar Combat Terminal’ project, traditional equipment yield plummeted to 68% at -35°C, while our Automatic OCR Lamination Equipment maintained 99% yield with thermal compensation, cutting project delivery time by 40%."* —Advanced Manufacturing 2025 Case Studies
Learn More,https://auto-odm.com/, Limited-Time Resource Pack (High-Conversion Design)
▸ Download the *2025 Multi-Scenario Lamination Whitepaper* (includes medical/automotive/military parameter templates)
▸ Apply for a Free Process Parameter Scan (upload product images for a customized solution)
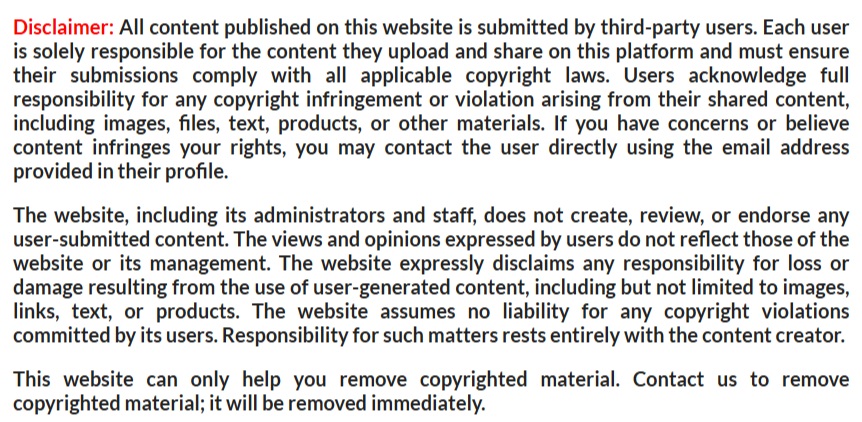