views
Manufacturers who master a lean manufacturing system without sacrificing output gain sizable competitive advantages that leave rivals in the dust. Most companies fear implementing lean manufacturing will disrupt operations, but the opposite happens when done correctly. Smart manufacturers discover implementing lean manufacturing accelerates production by eliminating hidden bottlenecks slowing down entire production lines drastically.
Step 1: Shadow Map Your Current State
The first step in implementing lean manufacturing is to shadow map your current state. To do this you will need to observe and document what happens in your process, not what you think should be happening. That entails spending three days tracing the path of products throughout your entire process. Use a stopwatch to time the handoffs, delays, and the interactions of each rework cycle, etc.
Most manufacturers are shocked to discover that nearly 40-60% of their total floor time consists of non-value-added activities that they were previously not aware of. Shadow mapping creates an awareness of where improvement opportunities exist, and at the same time does not stop production.
Step 2: Pick a Pilot Zone Strategy
Identify a few non-critical areas of production for your initial experimentation with implementing lean manufacturing. This should be any area where simple learning mistakes will not impact your customer delivery. The successful pilot project will typically involve approximately 10 - 15% of your total production capacity, allowing you to develop proof-of-concept without straying too much from your operation.
Additionally, document everything, as whatever is successful in a pilot will become the opportunity to deploy a company-wide rollout.
Step 3: Engaging Your Workforce Before Process Change
Implementing lean manufacturing will ultimately fail if your employees feel disengaged from collective decision-making. Perform floor-level problem identification sessions, and let your operators reveal their biggest frustrations each day. These sessions will typically generate over 200 improvement ideas in the first month. Once workers buy into solution development, they are your champions for implementation rather than resistors to change.
Step 4: Implementing Quick Wins
Quick wins are changes implemented over 30 days, including simple relocation of tools, elimination of pointless approval procedures, or modification of material flow patterns. The fast victories result from creating momentum as you demonstrate that implementing lean manufacturing raises rather than damages output. Measuring progress from start to finish is the simplest way and quite obviously shows considerable growth over surprisingly long periods.
Step 5: Standard Work Documentation
Standard work documentation is the process of documenting the optimized process immediately after implementation. Develop visual work documents showing the generated new way vs. the old way. Standard work documentation is vital in preventing reverting to inefficient practice and ensuring optimal, and reasonable consistency across shifts. Engage in documentation within 48 hours of making any change in process.
Step 6: Performance Measurement Systems
Establish accountability systems for measuring key metrics in real-time; for example: cycle time, defect rates, equipment run-time utilization, or actions resulting from employee suggestions made in the previous month. Implementing lean manufacturing is about making evidence-based decisions, as opposed to gut feelings. Digital dashboards that are updated hourly are invaluable for making decisions about correcting the course of your fluctuation in production before relatively small issues mushroom into major production crises.
Step 7: Building Continuous Improvement Culture
Lean manufacturing implies that the way it is implemented within the organization is more of an operational philosophy rather than merely something used for a period of a few weeks with clearly defined deadlines for project implementation. There should be monthly learning exchanges from department to department, daily huddles for improvement purposes, and weekly sessions for troubleshooting. Generally, if an organization stays with lean upgrades, most employee-generated ideas are implemented within sixty days, thereby maintaining momentum for continuous improvement.
The Technology Acceleration Factor
Next-generation implementing lean manufacturing utilizes a variety of digital tools that were not available to the original lean thinkers at Toyota. The accelerated advantage of IoT sensors, predictive analytics, workflow management, and control of internal processes can exponentially increase the ripples that traditional lean creates.
However, technology is best applied to well-performing processes as opposed to automating existing inefficient processes.
Warning Signs You May Be Heading for an Implementation Failure
Implementing lean manufacturing may be heading toward failure signaled by three ominous warning signs:
-
Swelling bureaucracy stifling improvement initiatives,
-
Dwindling employee suggestions,
-
Management fixating on cost-cutting over value creation
Tackle these issues pronto lest the entire initiative implodes spectacularly under the weight of accumulated problems and sheer bureaucratic ineptness.
Your Implementation Blueprint
The seven steps outlined here are effective because addressing process mechanics and human psychology simultaneously is crucial. Competitors either shy away from lean implementation altogether due to trepidation about production fallout or botch it miserably in execution. Methodically implementing lean manufacturing accelerates performance rather than hindering it through production-friendly approaches that create a sustainable competitive advantage.
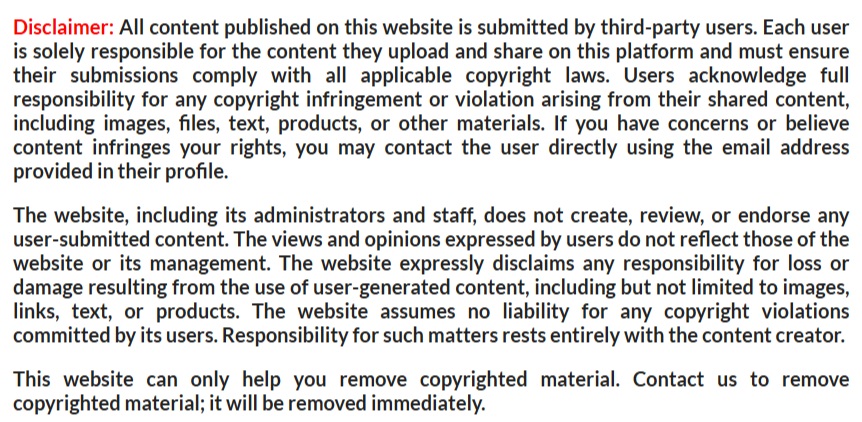