8
views
views
Explore the growing molded pulp packaging market as industries shift toward sustainable, biodegradable, and recyclable solutions. Discover trends, innovations, and global demand driving this eco-friendly packaging revolution.
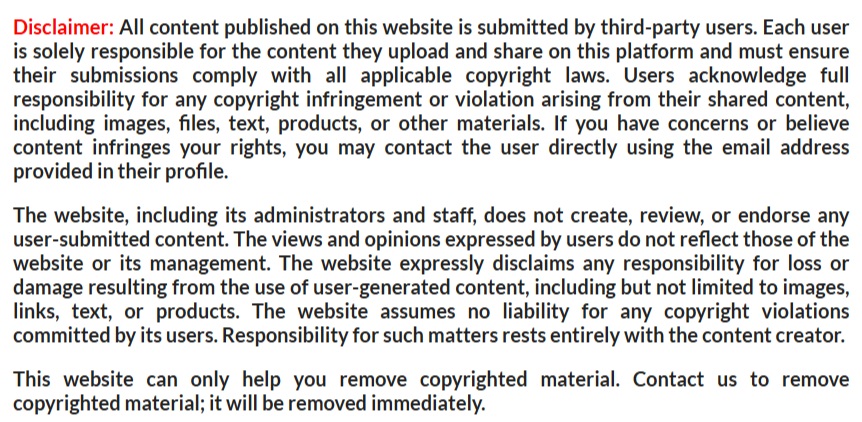