views
Market Overview
The global automotive aluminum market is witnessing accelerated growth, fueled by the rising preference for lightweight and fuel-efficient vehicles. In 2024, the market was valued at USD 32.6 billion and is anticipated to surge to USD 61.3 billion by 2033, registering a CAGR of 7.3% during the forecast period of 2025–2033. This upward trend is supported by the increasing demand for luxury and electric vehicles, heightened environmental awareness, and expanding collaborations between OEMs and leading aluminum producers.
Study Assumption Years
-
Base Year: 2024
-
Historical Years: 2019–2024
-
Forecast Years: 2025–2033
Automotive Aluminum Market Key Takeaways
-
Market Size & Growth: Reaching USD 32.6 billion in 2024, the market is projected to grow to USD 61.3 billion by 2033, reflecting a 7.3% CAGR during 2025–2033.
-
Product Form Leadership: Cast aluminum dominates due to its high strength-to-weight ratio and ease in forming intricate automotive components.
-
Vehicle Type Insight: Passenger cars account for the largest market share, propelled by emission control regulations and fuel economy requirements.
-
Application Focus: The powertrain segment leads the market, leveraging aluminum’s superior heat dissipation and weight reduction benefits.
-
Regional Spotlight: Asia Pacific commands the top position globally, backed by rising electric vehicle adoption, large-scale manufacturing, and technological R&D.
-
Growth Enablers: Strict emissions mandates, EV proliferation, and continuous progress in aluminum processing methods are key growth accelerators.
📄 Request for a sample copy of this report: https://www.imarcgroup.com/automotive-aluminium-market/requestsample
Market Growth Factors
1. Surge in Lightweight and Fuel-Efficient Vehicle Demand
Rising aluminum consumption is mostly driven by the automobile industry's move toward lighter construction. Its capacity to lower vehicle weight makes it a preferred material for car manufacturers following changing environmental standards as it improves general fuel economy and lowers emissions. Consumer demand for sustainable mobility choices helps to drive this trend even more.
2. Advancements in Aluminum Processing Technologies
Enhancement of the automotive applications of aluminum via casting, extrusion, and form process innovations has increased its adaptability and performance. Modern techniques enable makers to create highly complicated, long-lasting parts without compromising strength or safety, therefore bolstering aluminum's appeal as a great alternative to conventional steel parts.
3. Growth of the Electric Vehicle (EV) Sector
Aluminum use has been greatly increased by the fast growth in electric car manufacture. Aluminum helps range and efficiency by countering the extra weight of batteries given its light weight. Aluminum is increasingly used in components like battery enclosures, frames, and chassis structures, therefore rendering it absolutely necessary for next-generation car design.
Market Segmentation
Breakup by Product Form:
Cast Aluminum
-
Die Casting: Ideal for complex shapes such as engine casings.
-
Permanent Mold Casting: Used for high-strength parts like wheels.
-
Sand Casting: Suitable for larger components like engine blocks.
Rolled Aluminum
-
Aluminum Plate: Applied in structural parts needing strength and rigidity.
-
Aluminum Sheet: Commonly used for body panels and exterior fittings.
-
Aluminum Foil: Used in thermal and insulation systems like heat exchangers.
Extruded Aluminum
-
Designed for specific profiles such as support frames and side-impact bars.
Breakup by Vehicle Type:
-
Passenger Cars: Widely utilize aluminum for frames, engine parts, and panels.
-
Light Commercial Vehicles (LCV): Use aluminum to boost payload and mileage.
-
Heavy Commercial Vehicles (HCV): Apply aluminum in tanks, wheels, and other key components to improve efficiency.
Breakup by Application:
Powertrain
-
Pistons, Engine Blocks, Fuel Systems, Heat Shields, Heat Exchangers
Chassis and Suspension
-
Suspension Components, Wheels, Steering Systems, Brake Parts
Car Body
-
Body Structure, Roof and Trim, Interiors, Hang-On Parts (doors, hoods, etc.)
Breakup by Region:
-
North America (United States, Canada)
-
Asia Pacific (China, Japan, India, South Korea, Australia, Indonesia, Others)
-
Europe (Germany, France, United Kingdom, Italy, Spain, Russia, Others)
-
Latin America (Brazil, Mexico, Others)
-
Middle East and Africa
Regional Insights
Asia Pacific leads the global automotive aluminum market, primarily due to the region’s expanding electric vehicle ecosystem, an abundance of production facilities, and a strong focus on innovation. Countries such as China, Japan, and India are leveraging aluminum’s benefits to produce fuel-efficient, high-performance vehicles, meeting both consumer demand and environmental objectives.
Recent Developments & News
The industry is witnessing innovation across multiple fronts. Manufacturers are integrating collaborative robots and machine vision technologies into aluminum production lines to boost precision and productivity. Simultaneously, a clear industry shift from steel to aluminum components is underway, aligned with the dual objectives of reducing vehicle weight and meeting sustainability benchmarks.
Key Players
-
Alcoa Inc.
-
Novelis
-
Rio Tinto Alcan
-
Constellium
-
BHP
-
AMG Advanced Metallurgical
-
UACJ Corporation
-
Norsk Hydro ASA
-
Dana Holding Corporation
-
Progress-Werk Oberkirch AG
-
Jindal Aluminium
-
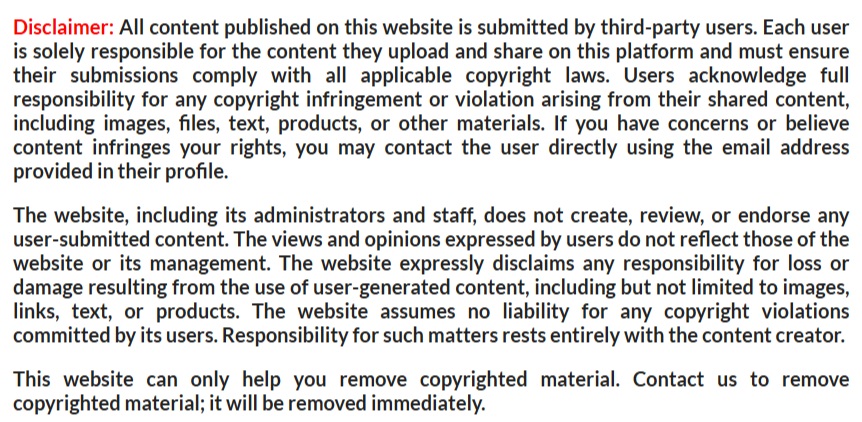