views
Cogeneration, also known as combined heat and power (CHP), is the simultaneous production of electricity and useful thermal energy from a single fuel source. Rather than discarding the heat that is normally wasted in conventional power generation, cogeneration systems capture and utilize this heat for industrial processes, space heating, and water heating. By capturing and using heat that would otherwise be wasted, cogeneration is a highly efficient process that can reduce primary energy usage by up to 40% compared to separate production of these forms of energy.
Main Components of a Cogeneration System
A typical cogeneration system consists of the following main components:
- Prime Mover: The prime mover generates the mechanical power that drives an electrical generator. Common prime movers include gas turbines, steam turbines, internal combustion engines, and microturbines.
- Electrical Generator: Connected to the prime mover, the generator converts mechanical power into electricity. Generators can be synchronous or induction types.
- Heat Recovery System: Captures waste heat from the prime mover exhaust and jacket cooling water. Common heat recovery components include heat recovery steam generators, Organic Rankine Cycle turbines, absorption chillers.
- Auxiliary Boilers: Used to produce additional process steam when waste heat recovery is insufficient. Fuel can include natural gas, biomass, municipal solid waste.
- Control System: Monitors and regulates system operation for optimal efficiency, safety and power quality. Control panels may integrate SCADA, PLCs and HMIs.
- Electrical Equipment: Includes switchgear, transformers and power conditioning needed to integrate with local utility grid. Uninterruptible power supply systems provide backup power.
Natural Gas Powered Cogeneration Systems
Natural gas is the most common fuel used in Cogeneration Equipment systems due to its widespread availability, low emissions, and high fuel efficiency / heat rates of modern gas engines and turbines. Some key natural gas cogeneration technologies include:
- Gas Turbines: Efficient and compact, gas turbines work well for large baseload cogeneration needs above 1 MW. Heat recovery steam generators boost efficiency. Combined cycle gas turbines reach up to 60% efficiency.
- Reciprocating Engines: Used for smaller cogeneration systems from 30 kW to 10 MW. Engines have lower capital cost and quick startup but require more maintenance. Combined heat and power efficiency commonly ranges from 75-85%.
- Microturbines: Even smaller units around 25-500 kW use compact combustion turbines. Used when space is restricted. Lower overall efficiency but easy maintenance enhances runtime. Can utilize low-grade waste heat very effectively.
Compared to grid electricity which averages around 33% efficiency when considering conversion and transport losses, modern natural gas cogeneration can realize up to 80% total system efficiency. This major improvement in efficiency translates directly to cost savings and reduced environmental impact.
Biomass Fueled Cogeneration for Renewable Energy
Biomass cogeneration provides a renewable alternative to fossil fuel systems by using sustainably sourced fuels such as wood waste, agricultural residues and landfill gas. The thermal efficiency is generally lower than gas fueled plants, but it is a carbon neutral technology that can contribute significantly to renewable energy goals.
Typical biomass cogeneration technologies include
- Steam Turbines: Large steam turbines above 5 MW thermal output are well suited for dedicated biomass power plants. Combined with backpressure turbines for additional power generation.
- Internal Combustion Engines: Similar to reciprocating gas engines but optimized to handle wood waste and crop residue fuels. Require specialized fuel handling and air pollution control systems.
- Gasification: Biomass is partially combusted with limited oxygen to produce a medium-BTU fuel gas. The gas can then fuel gas engines, gas turbines or microturbines for cogeneration. Provides fuel flexibility and higher efficiencies than direct combustion.
- Anaerobic Digesters: Produce biogas (methane and CO2) from organic wastes via bacterial fermentation. Biogas fuels genset cogeneration for waste/wastewater treatment plants and farms.
While biomass fuel supplies and technologies continue to develop, cogeneration plays an important role in providing clean, renewable baseload power to support sustainable economic growth. Hybrid systems that integrate biomass with natural gas are also gaining popularity for around-the-clock power generation.
Cogeneration Project Development Considerations
When considering a new cogeneration project, the following key factors must be evaluated to determine technical and economic feasibility:
- Thermal and Electrical Load Profiles: Cogeneration is best suited for facilities with matching thermal and power loads to maximize run hours and avoid curtailment of surplus power production.
- Fuel Availability and Cost: Fuel supply infrastructure and pricing will impact the overall cost-effectiveness of the project over its lifespan.
- Incentives and Policy Support: Grants, tax credits and favorable regulatory schemes for distributed generation can enhance project economics and payback timeline.
- Capital Expenditures: Equipment costs of the prime mover, generator, heat recovery system and balance of plant items determine the upfront investment needed for the cogeneration facility.
- Operations and Maintenance: Lifecycle costs involving fuel, labor and regular service/overhauls are considered in the economics analysis to identify the most cost-effective technology option.
- Emissions and Regulatory Compliance: Cogeneration emissions performance should meet all local air quality permits and regulations as well as proposed future standards.
Comprehensive technical and financial feasibility studies are required to minimize risks in project development and secure funding support for promising cogeneration opportunities. With careful evaluation and planning, the reliability, efficiency and cost savings benefits of cogeneration can be fully realized.
In , cogeneration equipment provides an efficient means of generating power and useful heat simultaneously from a single fuel source. By capturing waste heat that would otherwise be wasted, cogeneration significantly improves overall energy efficiency compared to separate generation of electricity and thermal energy. Modern natural gas and biomass cogeneration technologies
Get This Report in Japanese Language - コージェネレーション機器市場
Get This Report in Korean Language - 열병합 발전 장비 시장
About Author:
Vaagisha brings over three years of expertise as a content editor in the market research domain. Originally a creative writer, she discovered her passion for editing, combining her flair for writing with a meticulous eye for detail. Her ability to craft and refine compelling content makes her an invaluable asset in delivering polished and engaging write-ups.
(LinkedIn: https://www.linkedin.com/in/vaagisha-singh-8080b91)
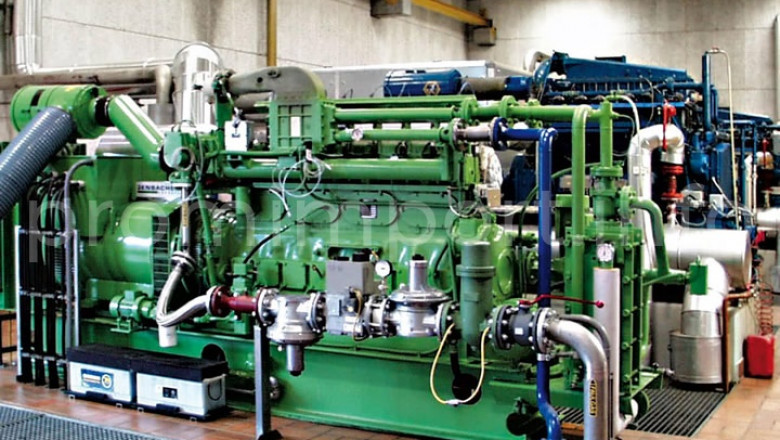

Comments
0 comment