Zinc Sulfite Manufacturing Plant Project Report 2025: Detailed Setup, Machinery, and Market Insights
Zinc Sulfite Manufacturing Plant Project Report 2025: Detailed Setup, Machinery, and Market Insights
Introduction
Zinc sulfite is a versatile chemical compound with a variety of industrial applications, ranging from water treatment and cosmetics to chemical manufacturing and agriculture. As industries increasingly require high-quality raw materials for diverse processes, the demand for zinc sulfite continues to rise globally. Establishing a zinc sulfite manufacturing plant is a promising venture for investors and entrepreneurs looking to tap into the growing chemical sector. A detailed zinc sulfite manufacturing plant project report is crucial to understand the technical, financial, and operational aspects involved in setting up a successful production unit.
This report will explore key aspects of the zinc sulfite manufacturing process, including market analysis, raw materials, production technology, machinery requirements, and financial considerations. By providing an in-depth look at these components, the report serves as a roadmap for setting up a zinc sulfite manufacturing plant.
Market Overview
Zinc sulfite has various applications across multiple industries, including metallurgy, agriculture, water treatment, and the production of other chemicals. It is used as a precursor in the synthesis of other zinc-based compounds, in the manufacturing of pigments, and as a stabilizer in the cosmetics and pharmaceutical industries. The growing demand for environmentally friendly chemicals and the need for better water management solutions have contributed to the increasing demand for zinc sulfite.
The global zinc sulfite market is witnessing steady growth, particularly in countries where industries like construction, automotive, and water treatment are flourishing. As zinc is an essential metal in many manufacturing processes, zinc sulfite plays a crucial role in several chemical and industrial applications.
Key Applications of Zinc Sulfite
- Water Treatment: Zinc sulfite is used in water purification and wastewater treatment as a reducing agent to eliminate harmful compounds.
- Agriculture: It is used in fertilizers and pesticides to enhance soil quality and control various plant diseases.
- Chemical Manufacturing: Zinc sulfite is an essential intermediate in the production of various zinc-based compounds like zinc oxide, zinc carbonate, and zinc sulfide.
- Cosmetics and Pharmaceuticals: Used as a stabilizer and a mild antiseptic in creams, lotions, and ointments.
Get a Free Sample Report with Table of Contents@
Raw Materials Required
The production of zinc sulfite primarily relies on raw materials that are either sourced from natural minerals or through chemical synthesis. The essential raw materials include:
1. Zinc Ore
Zinc sulfite is produced by reacting zinc-containing minerals, such as zinc oxide or zinc carbonate, with sulfur-containing compounds. Zinc ore, typically in the form of sphalerite (zinc sulfide), is a crucial raw material for the production process.
2. Sulfur Dioxide (SO2)
Sulfur dioxide is a key chemical reactant in the formation of zinc sulfite. It is commonly obtained from the combustion of sulfur or from the sulfur-containing gases released during the processing of ores.
3. Water
Water is used in various stages of the production process, including the dissolving and mixing of chemicals, as well as in cooling and washing stages.
4. Other Chemicals
Depending on the specific process used, additional chemicals such as acids or base solutions may be required to facilitate the chemical reaction and adjust the pH during production.
Machinery and Equipment
Setting up a zinc sulfite manufacturing plant requires specialized machinery for chemical processing, mixing, and filtration. Below is a list of key machinery and equipment needed:
1. Reactors
Chemical reactors are essential for mixing zinc-based materials with sulfur dioxide and other chemicals to produce zinc sulfite. These reactors must be capable of withstanding high temperatures and pressures.
2. Mixing Tanks
Mixing tanks are used to blend zinc ore with sulfur dioxide and water to initiate the chemical reaction that forms zinc sulfite. Proper agitation is required for uniform mixing.
3. Filtration Units
After the zinc sulfite is formed, filtration units are used to separate the liquid from any solid impurities or unreacted raw materials, ensuring the product is pure.
4. Drying Units
Once the zinc sulfite is separated and purified, drying units are necessary to remove excess water from the product, transforming it into a solid form for easier storage and packaging.
5. Packaging Machines
For distribution, the final product needs to be packaged in bags, containers, or other formats. Packaging machines fill, seal, and label the products for shipment.
Manufacturing Process
The manufacturing process of zinc sulfite involves several stages, from raw material preparation to the final packaging of the product. Here’s a step-by-step breakdown:
1. Preparation of Raw Materials
The process begins by preparing the raw materials, primarily zinc ore and sulfur dioxide. Zinc ore is crushed, and sulfur dioxide is typically produced through the combustion of sulfur or other sulfur-containing materials.
2. Chemical Reaction
Zinc ore (usually zinc oxide or zinc carbonate) is mixed with sulfur dioxide in a reactor. The sulfur dioxide reacts with the zinc compound in the presence of water, forming zinc sulfite (ZnSO3). This reaction is typically carried out under controlled conditions to achieve optimal yields.
3. Separation and Filtration
After the chemical reaction, the mixture is filtered to separate solid impurities, such as unreacted zinc ore, from the zinc sulfite. The liquid zinc sulfite is then separated and processed further.
4. Drying
The separated zinc sulfite is dried to remove excess moisture, leaving behind a powdery or solid form that is stable and ready for packaging.
5. Packaging
The final product is packaged into bags, drums, or containers for distribution to various industries that require zinc sulfite.
Financial Considerations
Starting a zinc sulfite manufacturing plant involves significant capital investment, along with ongoing operational costs. A comprehensive financial analysis is essential to ensure the plant’s success. The key financial aspects to consider include:
1. Capital Investment
The initial capital required for establishing a zinc sulfite plant includes the cost of land, plant construction, machinery, and equipment. This will vary depending on the plant's scale and location.
2. Raw Material Costs
The price of raw materials, especially zinc ore and sulfur dioxide, plays a significant role in determining production costs. Efficient sourcing and supply chain management are key to maintaining cost-effectiveness.
3. Operational Costs
Ongoing operational expenses include labor, utilities (electricity, water), maintenance, and other overheads. The plant’s energy consumption is particularly high in the reaction and drying stages, so energy efficiency is crucial for reducing costs.
4. Revenue and Profitability
Revenue projections depend on the plant’s production capacity, market demand, and pricing strategies. Conducting a detailed market analysis can help forecast potential revenue streams.
5. Cost of Distribution and Marketing
To reach potential buyers in industries such as water treatment, agriculture, and cosmetics, distribution costs (shipping, logistics) and marketing costs must be factored into the overall business plan.
Location Selection
Choosing the right location for the zinc sulfite manufacturing plant is crucial for ensuring cost-effectiveness and operational efficiency. Key factors to consider include:
- Proximity to Raw Material Suppliers: The plant should be located near zinc ore suppliers or sources of sulfur dioxide to reduce raw material transportation costs.
- Availability of Skilled Labor: Skilled workers, particularly those with expertise in chemical manufacturing, should be available in the region.
- Infrastructure: The site should have access to reliable electricity, water, transportation, and waste disposal systems.
- Regulatory Compliance: The location should adhere to local environmental and safety regulations to minimize legal risks.
Key Challenges
While the zinc sulfite manufacturing industry offers potential, there are several challenges to overcome:
1. Supply Chain Disruptions
Zinc ore and sulfur dioxide are essential raw materials, and fluctuations in their availability or price can affect production. Establishing reliable and cost-effective supply chains is critical.
2. Environmental Regulations
Zinc sulfite production involves the use of chemicals and generates waste by-products that need to be managed responsibly. Complying with environmental regulations is essential to avoid penalties and ensure sustainability.
3. Market Competition
The zinc sulfite market is competitive, with many manufacturers supplying to different industries. Differentiating the product by offering higher quality, better customer service, or innovative applications can help maintain a competitive edge.
FAQ
1. What are the key raw materials needed for zinc sulfite production?
The primary raw materials are zinc ore (typically zinc oxide or zinc carbonate), sulfur dioxide, water, and other chemicals as required for the process.
2. What machinery is required for zinc sulfite production?
Key machinery includes reactors, mixing tanks, filtration units, drying units, and packaging machines.
3. What industries use zinc sulfite?
Zinc sulfite is used in water treatment, agriculture (fertilizers and pesticides), chemical manufacturing, and cosmetics.
4. What is the manufacturing process for zinc sulfite?
The process involves preparing raw materials, reacting zinc ore with sulfur dioxide, separating impurities, drying the product, and packaging it for distribution.
5. How much capital is required to set up a zinc sulfite manufacturing plant?
Capital investment varies based on plant size, location, and equipment. Detailed financial planning is essential for accurate cost estimation.
Media Contact
Company Name: Claight Corporation
Contact Person: Lewis Fernandas, Corporate Sales Specialist — U.S.A.
Email: sales@expertmarketresearch.com
Toll Free Number: +1–415–325–5166 | +44–702–402–5790
Address: 30 North Gould Street, Sheridan, WY 82801, USA
Website: www.expertmarketresearch.com
Aus Site: https://www.expertmarketresearch.com.au
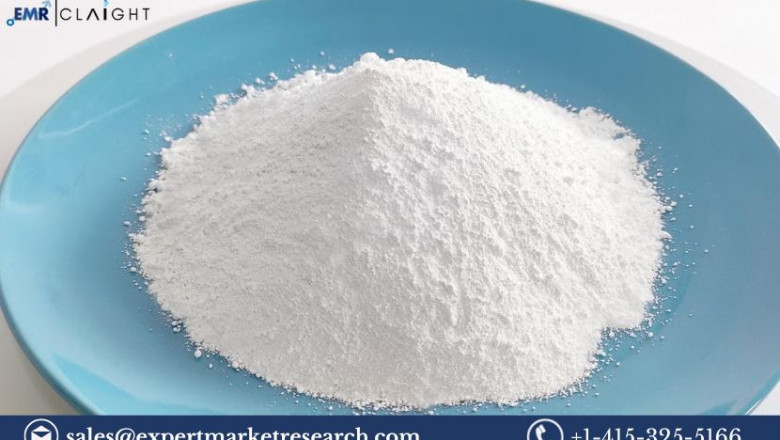

Comments
0 comment