views
Two Component Epoxy System Manufacturing Plant Project Report: Comprehensive Guide to Setup and Production
Two-component epoxy systems are versatile adhesives and coatings used across industries such as construction, automotive, aerospace, electronics, and manufacturing. These systems consist of a resin and a hardener that, when mixed, create a strong, durable, and resistant bond or coating. Known for their excellent adhesion, chemical resistance, and versatility, epoxy systems are indispensable in both industrial and consumer applications. Setting up a two-component epoxy system manufacturing plant requires an understanding of the production processes, equipment, and regulatory compliance to deliver high-quality products that meet industry demands.
Understanding Two-Component Epoxy System Production
The production of two-component epoxy systems involves sourcing high-quality raw materials, formulating the resin and hardener components, and ensuring precise packaging for user convenience. The process is designed to maintain the integrity and performance of the product across different applications.
-
Raw Material Selection
The primary materials include epoxy resin (such as bisphenol A or F-based resins), hardeners (like amines or anhydrides), fillers, and additives. Each material is selected based on the intended application, such as adhesives, coatings, or sealants. -
Formulation and Mixing
The epoxy resin is formulated with specific additives to achieve desired properties like viscosity, curing time, and adhesion. Similarly, the hardener is blended with appropriate activators and modifiers. Precise ratios are critical for optimal performance. -
Quality Control
Samples from each batch are tested for key properties such as viscosity, curing characteristics, mechanical strength, and chemical resistance. This ensures the product meets industrial standards and customer specifications. -
Packaging and Labeling
The two components are packaged separately to maintain stability until use. Packaging solutions like cartridges, cans, or pails are used, depending on the application. Proper labeling includes mixing ratios, safety information, and usage instructions. -
Storage and Distribution
The final products are stored in temperature-controlled conditions to preserve their shelf life and quality. Efficient distribution channels are established to ensure timely delivery to customers.
Get a Free Sample Report with Table of Contents@ https://www.expertmarketresearch.com/prefeasibility-reports/two-component-epoxy-system-manufacturing-plant-project-report/requestsample
Key Requirements for Setting Up a Manufacturing Plant
-
Location and Infrastructure
The plant should be located in an industrial zone with access to utilities such as electricity and water. Adequate space is required for production units, raw material storage, and administrative functions. -
Machinery and Equipment
Essential equipment includes mixing tanks, dispersers, filling machines, and quality testing instruments. Automation enhances consistency, productivity, and cost efficiency. -
Raw Material Procurement
Establishing a reliable supply chain for high-quality raw materials is crucial for uninterrupted production. Partnering with certified suppliers ensures consistent quality. -
Workforce and Training
Skilled personnel are required to operate machinery, monitor production processes, and perform quality checks. Regular training ensures adherence to safety standards and best practices. -
Regulatory Compliance
Compliance with environmental regulations, safety standards, and industry certifications is essential. Proper documentation and audits are necessary for legal operations and market entry.
Applications of Two-Component Epoxy Systems
-
Construction
Epoxy systems are used for structural bonding, floor coatings, and repairs, providing durability and resistance to environmental factors. -
Electronics
In electronics, epoxy systems are used for encapsulation, potting, and coating to protect sensitive components from moisture and mechanical stress. -
Automotive and Aerospace
Epoxy adhesives play a crucial role in bonding and sealing parts in vehicles and aircraft, offering high strength and lightweight solutions. -
Industrial Maintenance
Epoxy systems are widely used in industrial settings for corrosion protection, pipeline repair, and machinery bonding. -
Consumer Applications
These systems are used in DIY projects, crafts, and household repairs, offering easy-to-use solutions for bonding and sealing.
Benefits of Establishing a Two-Component Epoxy System Manufacturing Plant
-
High Market Demand
The growing use of epoxy systems across industries drives consistent demand, ensuring a stable and lucrative market. -
Versatility in Applications
Two-component epoxy systems cater to a wide range of applications, from heavy industrial uses to everyday consumer needs. -
Innovation Opportunities
Manufacturers can develop specialized formulations tailored to specific applications, such as quick-curing adhesives or high-temperature coatings. -
Sustainability Potential
By adopting eco-friendly practices and raw materials, manufacturers can appeal to environmentally conscious markets and enhance brand reputation.
Manufacturing Challenges
-
Raw Material Costs
The cost of epoxy resins and hardeners can fluctuate, impacting production costs. Efficient procurement strategies can help mitigate this challenge. -
Regulatory Requirements
Meeting stringent environmental and safety regulations requires careful planning and adherence to compliance standards. -
Product Differentiation
The epoxy market is competitive, requiring continuous innovation and marketing to stand out. -
Quality Assurance
Ensuring consistent quality across production batches is critical to maintaining customer trust and meeting industrial standards.
Future Trends in Two-Component Epoxy Systems Manufacturing
The two-component epoxy market is poised for growth with advancements in materials science and application technologies. Key trends include the development of bio-based and low-VOC (volatile organic compound) formulations to meet sustainability goals. Smart epoxies with self-healing and conductive properties are gaining traction in advanced applications like electronics and aerospace. The rise of automated dispensing systems for precision applications is also driving demand. Manufacturers focusing on eco-friendly practices, innovation, and customized solutions are expected to lead the market.
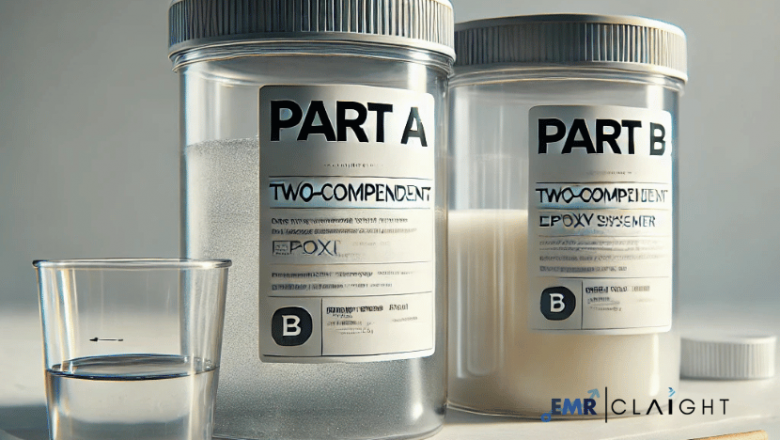

Comments
0 comment