views
Introduction
The France CNC Drilling Machine Market is experiencing a significant transformation, driven by the emergence of Industry 4.0 technologies. With the integration of automation, the Internet of Things (IoT), and Artificial Intelligence (AI), the landscape of manufacturing in France is evolving rapidly. As manufacturers strive to improve precision, reduce costs, and enhance productivity, CNC drilling machines have become central to their operations. This article explores how the latest technological advancements in Industry 4.0 are influencing the CNC drilling machine market in France, why the market is trending, and what the future holds for this key sector of the manufacturing industry.
What is CNC Drilling and Its Importance in Manufacturing?
CNC (Computer Numerical Control) drilling machines are an essential part of modern manufacturing processes. These machines are designed to automate drilling operations, providing high precision and efficiency. CNC drilling machines are used in various industries, including aerospace, automotive, electronics, and construction. Their ability to produce intricate designs, operate with minimal human intervention, and maintain consistent quality makes them invaluable in today's competitive market.
The significance of CNC drilling machines lies in their ability to enhance production capabilities. They are not only faster and more accurate than manual machines, but they also allow for complex, high-tolerance holes to be drilled with ease, making them ideal for mass production.
How Industry 4.0 is Impacting the France CNC Drilling Machine Market
Industry 4.0 is the name given to the current trend of automation and data exchange in manufacturing technologies. It involves the integration of various advanced technologies, such as AI, IoT, machine learning, big data, and cloud computing, to create “smart factories.” This transformation has far-reaching implications for sectors like CNC drilling machines, particularly in France.
1. Automation and Smart Control Systems
Automation is one of the cornerstones of Industry 4.0. In the CNC drilling market, the integration of automated systems significantly improves operational efficiency. CNC drilling machines are now being equipped with advanced automation technologies that enable faster production cycles, less downtime, and more precise drilling operations.
Manufacturers in France are increasingly adopting automated systems that reduce human error, lower labor costs, and increase the overall efficiency of manufacturing lines. By implementing smart control systems, manufacturers can remotely monitor the performance of CNC drilling machines, predict maintenance needs, and optimize the production process in real-time.
2. Internet of Things (IoT) and Data Exchange
The integration of IoT in CNC drilling machines is one of the most notable impacts of Industry 4.0. IoT allows these machines to connect to a network and communicate with other machines and systems within the factory. This networked environment allows for the seamless exchange of data and real-time monitoring, enabling manufacturers to make informed decisions about production schedules, machine performance, and maintenance.
In the context of the France CNC drilling machine market, IoT-enabled machines provide manufacturers with actionable insights into their production processes. By gathering data from CNC drilling machines, IoT systems help optimize workflows, reduce waste, and increase uptime. Additionally, IoT-based predictive maintenance can identify potential issues before they cause significant downtime, ultimately improving productivity and reducing operational costs.
3. Artificial Intelligence (AI) and Machine Learning
AI and machine learning are crucial for advancing the capabilities of CNC drilling machines in France. These technologies enable CNC machines to “learn” from historical production data, making intelligent adjustments to optimize drilling operations. AI algorithms can predict and adjust parameters such as speed, feed rates, and tool paths based on real-time conditions, ensuring that each operation is completed with minimal waste and maximum efficiency.
Furthermore, AI plays a key role in improving quality control. By analyzing data from various sensors and cameras, AI systems can detect defects or irregularities in the drilling process, enabling manufacturers to make immediate adjustments before problems affect the final product. This real-time quality assurance ensures that only high-quality parts are produced, reducing the need for rework and scrap.
4. Cloud Computing and Big Data
Cloud computing and big data analytics are central to the implementation of Industry 4.0 in the CNC drilling machine market. Manufacturers in France are leveraging cloud platforms to store, analyze, and access vast amounts of data generated by CNC machines. These cloud-based systems allow for greater collaboration, as teams can access real-time data and performance metrics from anywhere in the world.
Big data analytics enables manufacturers to uncover trends, optimize processes, and predict future performance. By analyzing large datasets from CNC drilling machines, manufacturers can identify inefficiencies, predict maintenance schedules, and enhance decision-making. This data-driven approach ensures continuous improvements in production processes and supports long-term business strategies.
5. Advanced Materials and New Design Capabilities
The adoption of Industry 4.0 technologies has also allowed for more advanced materials to be used in CNC drilling processes. With the help of AI and machine learning, manufacturers can now work with harder materials and produce more intricate designs. This is particularly important in industries like aerospace and automotive, where precision and durability are critical.
CNC drilling machines, now equipped with advanced sensors and real-time feedback loops, can work with materials that were previously difficult to handle. By combining these machines with AI-based systems, manufacturers can explore new design possibilities, leading to innovations in products and applications that were not possible before.
Why the France CNC Drilling Machine Market is Trending
The France CNC drilling machine market is trending for several key reasons, primarily driven by the advancements of Industry 4.0. Let’s examine why this sector is gaining attention:
1. Increased Demand for Precision Manufacturing
As global industries demand higher precision and faster turnaround times, CNC drilling machines have become indispensable. France, as a leader in sectors like aerospace, automotive, and electronics, is particularly focused on meeting these demands. The ability to produce components with extreme accuracy and minimal error is essential in these industries, and CNC drilling machines provide the perfect solution.
2. Rising Need for Automation and Efficiency
Manufacturers in France are increasingly seeking ways to automate their processes and improve operational efficiency. The integration of automation into CNC drilling machines, combined with the ability to gather and analyze data through IoT and AI, helps companies reduce manual labor, minimize errors, and increase productivity. As labor shortages and rising costs put pressure on manufacturers, automation is no longer just an option—it’s a necessity.
3. Sustainability and Cost-Effectiveness
With growing concerns about sustainability and environmental impact, manufacturers in France are looking for ways to optimize their production processes to be more energy-efficient and resource-efficient. Industry 4.0 technologies help reduce material waste, minimize energy consumption, and lower the carbon footprint of manufacturing processes. As companies adopt these technologies, they also gain a competitive edge by meeting sustainability goals and operating more cost-effectively.
4. Competitive Advantage and Innovation
In France, the growing adoption of Industry 4.0 technologies in CNC drilling machines is also a direct response to the increasing global competition. Manufacturers are investing in these advanced technologies to stay competitive, ensure faster production cycles, and deliver higher-quality products. The ability to innovate and continuously improve production capabilities is driving demand for CNC drilling machines that are equipped with the latest Industry 4.0 technologies.
The Future of the France CNC Drilling Machine Market
As Industry 4.0 continues to evolve, the France CNC drilling machine market is poised for significant growth. The future of this market will be shaped by several factors, including the increased integration of AI, IoT, and advanced automation technologies. In the coming years, we can expect even greater advancements in machine learning algorithms, predictive maintenance, and data analytics.
Manufacturers in France will likely continue to embrace Industry 4.0 technologies to stay ahead in the global manufacturing race. Additionally, the development of new materials, combined with cutting-edge CNC drilling machines, will open up new possibilities for industries such as aerospace and automotive, further driving demand for these machines.
Conclusion
The France CNC Drilling Machine Market is undergoing a transformative shift thanks to the influence of Industry 4.0 technologies. The integration of AI, IoT, automation, and big data is not only enhancing the efficiency and precision of CNC drilling machines but also revolutionizing the way manufacturers in France approach production. As manufacturers seek to remain competitive, reduce costs, and improve sustainability, the demand for advanced CNC drilling machines is expected to continue rising.
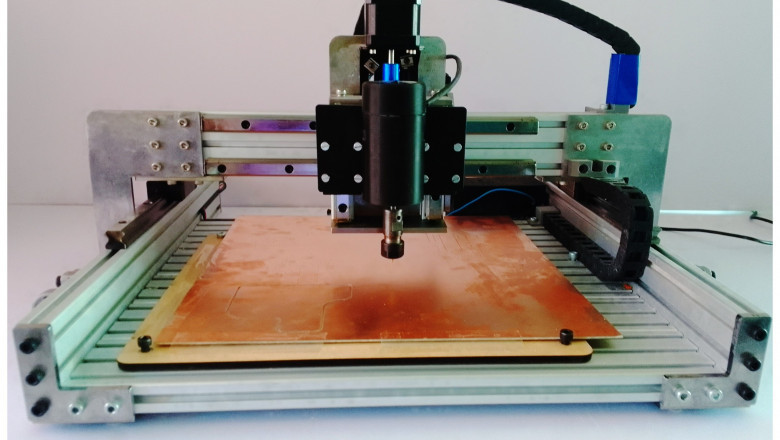
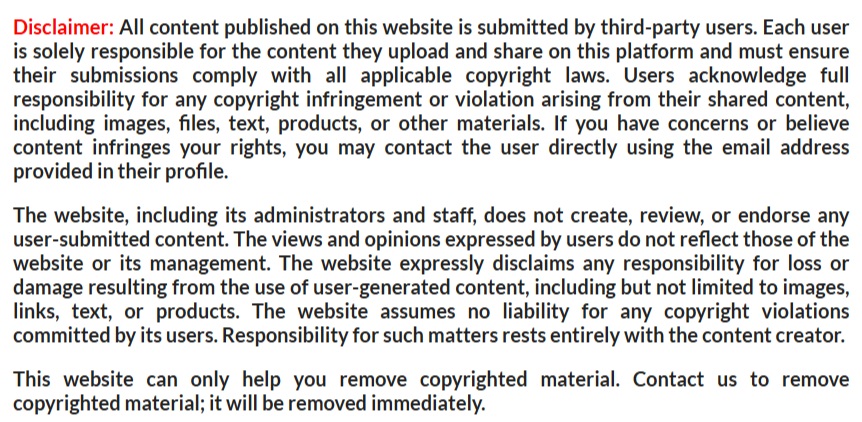
Comments
0 comment