views
Introduction
The Indonesia Ceramic Machinery Market is one of the leading sectors in the country’s manufacturing landscape, bolstered by a rising demand for high-quality products in construction, home décor, and industrial applications. With technological advancements influencing various industries globally, the integration of the Internet of Things (IoT) in ceramic production is transforming how ceramics are manufactured, managed, and delivered.
This article explores the growing adoption of IoT in the Indonesian ceramic machinery market, its impact on production efficiency, and the promising opportunities it presents for the future.
Click Here For Your FREE Sample!
The Growing Ceramic Industry in Indonesia
Indonesia’s ceramic industry has been expanding steadily, driven by both local demand and international exports. As the third-largest producer of ceramics in Southeast Asia, Indonesia’s market is characterized by a diverse range of products, from tiles and sanitary ware to decorative and functional ceramics. The country’s booming construction and real estate sectors contribute significantly to this growth, pushing manufacturers to innovate and optimize production processes.
The increasing need for higher quality and cost-effective products has led manufacturers to seek solutions that streamline operations and improve product quality. With this, the integration of IoT in ceramic production processes has emerged as a game-changer, offering enhanced automation, real-time data monitoring, and predictive maintenance features that are crucial for competitive survival in the modern market.
Understanding IoT and Its Role in Ceramic Production
The Internet of Things (IoT) refers to the network of interconnected devices embedded with sensors, software, and other technologies that collect, exchange, and analyze data to improve decision-making and operational efficiency. In the ceramic industry, IoT applications are proving to be highly beneficial, allowing for greater automation, enhanced control over production processes, and real-time data analysis to optimize efficiency.
IoT technologies enable manufacturers to monitor key production parameters remotely, analyze data for better decision-making, and ensure that the machinery and processes are running at optimal performance levels. These advancements have significant implications for Indonesian ceramic manufacturers, who are increasingly integrating IoT-enabled devices in various stages of the production line.
How IoT Integration Improves Ceramic Manufacturing Efficiency
The introduction of IoT technology in ceramic production has improved various aspects of manufacturing, from machinery performance to quality control. Smart machines, which include IoT sensors, provide real-time insights into production processes and equipment status, allowing operators to identify potential issues before they lead to costly downtime or defects.
One of the primary benefits of IoT integration is the ability to monitor production parameters such as temperature, humidity, pressure, and machine performance. This data can help identify trends, inefficiencies, or potential areas for improvement, allowing operators to make adjustments on the fly. This increased visibility can reduce waste, lower energy consumption, and streamline operations.
Predictive Maintenance and Its Benefits
One of the most important applications of IoT in ceramic machinery is predictive maintenance. Traditional maintenance practices are often reactive, where manufacturers wait for equipment to break down before performing repairs. This can result in expensive downtime and delays in production schedules.
With IoT-powered predictive maintenance, ceramic manufacturers in Indonesia can track the performance of key equipment in real time. Sensors monitor parameters such as vibration, temperature, and pressure, allowing the system to detect anomalies that might indicate an impending failure. This data enables manufacturers to perform maintenance tasks only when needed, reducing unnecessary downtime and avoiding costly repairs. By fixing issues before they become serious problems, manufacturers can extend the lifespan of their machinery and maintain a more consistent production schedule.
Enhancing Quality Control with IoT
Quality control is a critical component of ceramic production. Ceramic products, particularly tiles and sanitary ware, need to meet specific quality standards in terms of size, color, surface texture, and durability. Traditionally, quality control was handled manually, requiring inspectors to visually check products for defects. However, this process can be time-consuming and prone to human error.
IoT-enabled quality control systems are revolutionizing this process. Using cameras, sensors, and advanced algorithms, IoT devices can continuously monitor products for defects during the manufacturing process. Vision systems and AI-powered analytics can detect cracks, chips, or color inconsistencies in real-time. Automated quality control systems not only ensure higher product quality but also reduce the reliance on manual labor, leading to faster production cycles and reduced operational costs.
Energy Efficiency and Sustainability through IoT
Energy consumption is one of the most significant operational costs for ceramic manufacturers, particularly in processes such as kiln firing and drying. The integration of IoT allows manufacturers to optimize energy usage, which is crucial in an energy-intensive industry like ceramics. By monitoring and controlling energy consumption in real-time, manufacturers can identify areas where energy use can be reduced or optimized.
IoT sensors can monitor kiln temperatures, firing cycles, and power usage, ensuring that the equipment operates at maximum efficiency. Additionally, IoT systems can analyze energy consumption patterns over time, helping manufacturers adjust production schedules and processes to minimize energy waste. These improvements not only reduce operational costs but also contribute to sustainability efforts by lowering the environmental impact of ceramic production.
Automation in the Ceramic Industry
Automation plays a critical role in the modern ceramic industry, allowing manufacturers to enhance efficiency and maintain consistent product quality. IoT is a key enabler of automation in ceramic production. Automated systems, including robots and conveyors, are increasingly being used for tasks such as material handling, glazing, and packaging.
IoT-enabled automation systems allow for seamless communication between different stages of production. For example, automated robots can transport products from one machine to another, while sensors track the progress of each product through the manufacturing process. This level of automation reduces human intervention, speeds up production cycles, and helps manufacturers meet the growing demand for high-quality ceramic products.
Supply Chain and Inventory Management with IoT
In addition to improving the production process, IoT also offers significant benefits in supply chain and inventory management. By tracking raw materials, finished products, and shipments in real-time, manufacturers can gain full visibility into their operations and optimize their inventory management practices.
IoT sensors attached to raw materials and products can monitor the location, condition, and quantity of items at every stage of the supply chain. For instance, inventory systems can automatically track stock levels, reorder supplies when necessary, and ensure that materials arrive just in time for production. This helps prevent overstocking, stockouts, and production delays, resulting in a more efficient and cost-effective supply chain.
Overcoming Challenges in IoT Integration
While the benefits of IoT integration in ceramic production are significant, there are also challenges that Indonesian manufacturers must address. One of the primary obstacles is the cost of adopting IoT technologies. For many manufacturers, especially small and medium-sized enterprises (SMEs), the initial investment required to implement IoT systems can be a barrier.
Additionally, the complexity of integrating IoT solutions into existing production systems can be overwhelming. Manufacturers need to invest in specialized skills and training to ensure that their employees are capable of managing and interpreting the data generated by IoT devices.
Despite these challenges, the long-term benefits of IoT integration—such as improved efficiency, reduced downtime, and enhanced product quality—are pushing more ceramic manufacturers in Indonesia to adopt these technologies. Government support for digital transformation and Industry 4.0 initiatives will also play a key role in accelerating IoT adoption in the ceramic industry.
Future Outlook for IoT in the Indonesian Ceramic Machinery Market
Looking ahead, the role of IoT in the Indonesian ceramic machinery market is expected to continue growing. As technology advances, the capabilities of IoT devices will expand, enabling even more sophisticated applications in manufacturing processes. The rise of 5G technology will further enhance IoT’s potential by offering faster data transfer speeds, which is crucial for real-time monitoring and decision-making on the production floor.
The Indonesian government’s push toward Industry 4.0 and smart manufacturing is likely to accelerate the adoption of IoT in the ceramic industry. With continued investment in digital technologies, Indonesian manufacturers will be well-positioned to improve their global competitiveness and meet the evolving demands of both domestic and international markets.
Conclusion
The integration of IoT in the Indonesian ceramic machinery market is transforming the way ceramics are produced, offering significant advantages in terms of efficiency, quality control, energy management, and automation. While challenges such as high initial costs and the need for skilled labor remain, the long-term benefits of IoT adoption outweigh these concerns.
As technology continues to evolve and the demand for smart manufacturing increases, Indonesian ceramic manufacturers are poised to leverage IoT to stay competitive in the global market. With the continued growth of the industry and the adoption of Industry 4.0 initiatives, the future of ceramic production in Indonesia looks promising and highly automated.

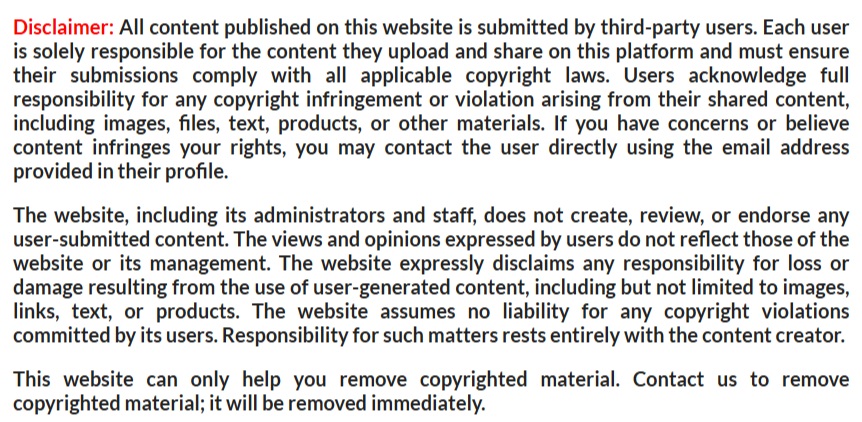
Comments
0 comment