views
Introduction: Why Custom Foam Inserts Matter
When it comes to protecting sensitive equipment, expensive tools, or valuable products, one size does not fit all. That’s where custom foam inserts come in. These tailored solutions are more than just padding—they’re engineered protection systems designed to cradle, shield, and secure items from damage, movement, and wear.
From aerospace components to luxury electronics, custom foam inserts have become an essential part of packaging and logistics in the USA. In this guide, we’ll explore everything you need to know to make an informed decision, whether you’re a business owner, logistics manager, or design engineer.
What Are Custom Foam Inserts?
Custom foam inserts are specially cut or molded foam components designed to fit around a specific product or group of items. Unlike generic or off-the-shelf padding, these inserts are tailored to the exact shape and specifications of your products, offering superior protection, organization, and presentation.
These inserts are used across many industries including:
-
Electronics
-
Aerospace
-
Automotive
-
Medical
-
Retail
Top 10 Factors to Consider When Choosing Foam Inserts
1. Material Type
The most common foam types include:
-
Polyethylene (PE) – rigid, durable, water-resistant
-
Polyurethane (PU) – softer, ideal for cushioning
-
Cross-linked PE – closed-cell, great for high-end applications
-
EVA Foam – lightweight, flexible, shock absorbent
2. Foam Density
Higher density foams provide better support and protection. Lighter foams are cost-effective but may offer less impact resistance. Consider your product's fragility when selecting density.
3. Customization Capabilities
Laser cutting, waterjet cutting, and CNC routing allow for precise customization. Choose a supplier who can offer multi-layer designs, color options, and branding elements.
4. Protective Qualities
Is your item sensitive to shock, vibration, or static? Look for features like:
-
Anti-static foam
-
Vibration dampening
-
Temperature resistance
5. Application or Industry Use
Each industry has specific needs:
-
Electronics need anti-static protection
-
Medical tools need hygienic, cleanable inserts
-
Luxury goods require aesthetic finesse
6. Water & Chemical Resistance
In harsh environments, especially outdoors or in transit, water resistance is a must. Cross-linked polyethylene and EVA foam perform well in these conditions.
7. Compliance Standards
Does your packaging need to meet specific certifications like MIL-SPEC, ISO, or RoHS? Choose a manufacturer who understands and adheres to those guidelines.
8. Aesthetics and Branding
Foam inserts can reflect your brand’s quality. Colored foam, printed logos, and stylish die-cuts elevate the unboxing experience.
9. Budget Constraints
While custom foam inserts are an investment, they save money in the long run by reducing returns, breakage, and warranty claims. Work with a supplier who balances quality and affordability.
10. Supplier Reputation
Look for a USA-based foam manufacturer with excellent reviews, responsive customer service, and proven experience across your industry. Don't hesitate to ask for references or samples.
Popular Industries Using Custom Foam Inserts
Aerospace and Defense
Foam inserts are used for avionics, drones, communication devices, and high-value tools. Durability and MIL-SPEC compliance are critical.
Electronics and Tech
From circuit boards to cameras, electronics demand static-dissipative foam. Inserts are shaped to prevent micro-movements that lead to damage.
Medical and Healthcare
Clean, sterile foam is ideal for surgical tools and diagnostic devices. Inserts can be easily sanitized and organized.
Automotive and Motorsports
Tools, diagnostic equipment, and racing components stay secure with high-density inserts. Custom cutouts make inventory and transport simple.
Retail and Consumer Products
Luxury items like watches, perfumes, and glassware are showcased beautifully in foam inserts that combine protection and presentation.
Benefits of Using Custom Foam Inserts
Enhanced Protection
Protect against:
-
Shock
-
Vibration
-
Moisture
-
Electrostatic discharge (ESD)
Professional Presentation
Custom foam elevates the visual appeal of packaging. This is crucial for marketing, unboxing videos, and customer satisfaction.
Long-Term Cost Savings
Reduce:
-
Product returns
-
Replacement costs
-
Repair fees
-
Warehouse damage
Foam Types Explained
Polyethylene (PE) Foam
-
Closed-cell
-
Durable
-
Great for toolboxes and cases
Polyurethane (PU) Foam
-
Open-cell
-
Soft cushioning
-
Suitable for light, delicate items
Cross-linked PE Foam
-
Closed-cell, higher strength
-
Smooth surface for luxury packaging
Anti-static Foam
-
Prevents ESD
-
Ideal for electronics and semiconductors
How to Measure and Design Your Custom Inserts
-
Measure Dimensions: Length, width, height, and contour.
-
Consider Grouping: Keep similar items together.
-
Use Templates or CAD Files: For precision.
-
Decide Layering: Multi-layer foam can add extra protection.
-
Visual Mockups: Confirm design before production.
Manufacturing Process of Foam Inserts
-
Consultation & Design
-
Material Selection
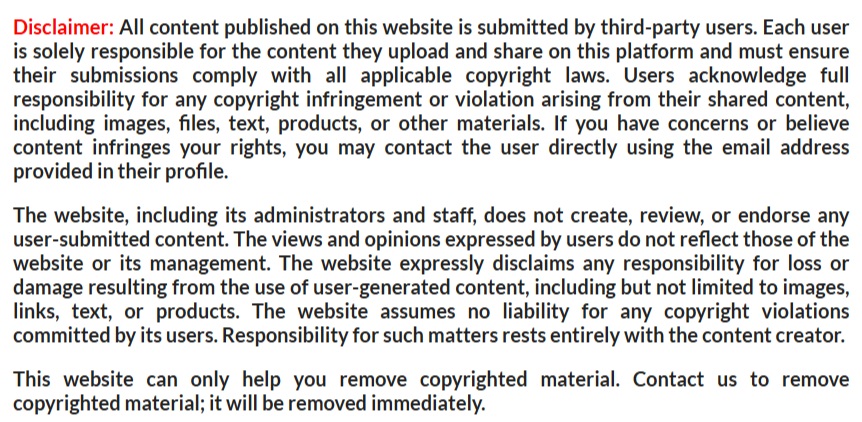