views
box compression tester
Transportation can be hard on packaging, while packaging protects the products. As a result, the apparatus called a box compression tester is used to assess the strength and durability of packaging materials, like corrugated cardboard boxes, under the box compression test. The boxing-up test machine must place enough boxes on it so that they can withstand the extra weight damage caused to a product during storage and transport. This is a guide to using the box compression test machine to improve packaging performance.
What is a Box Compression Test?
A Box Compression Test is defined as the test used to determine the ability of boxes to resist crushing under compressive force. The machine compresses the box until it either deforms or collapses, simulating the forces that the boxes will experience during stacking or shipping. The gist of the test is to determine the loading that a box can withstand just before failure, thus providing a manufacturer the hit information concerning the structural performance of a box.
How to Operate a Box Compression Tester: A Step-by-Step Guide
Step 1: Prepare Your Sample for Testing
Select any box that conforms to the regular findings of your packing process. Make sure that it is assembled as per the production specifications. Important considerations include:
-
Dimensions of the box (length, width, and height)
-
Type and thickness of the cardboard
-
Type of flute (single-wall or double-wall)
-
Design of the flap and closure procedure (tape or glue)
Do not use boxes with defects or damage, as these may influence the test results.
Step 2: Set Up Your Testing Machine
Check the cleanliness and calibration of the machine before operation. The two opposing parallel compression plates must have been perfectly aligned without any obstructions.
Now set the required test parameters:
-
Compression Speed: Control on compression speed, which could hardly exceed between 0.5 to 2 in/min based on the given industrial requirements.
-
Force Limits: Select a maximum force limit to prevent the machine or the box from irreversible destruction beyond its collapsing point.
Make sure that these settings abide by the test standards as required (ISO, ASTM, etc.).
Step 3: Now Place Your Box Onto an Appropriately Designed Platform For Testing
Put the box on the testing platform with the utmost care, ensuring it's flat and centered between the compression plates. The alignment must be impeccable to achieve consistent and accurate results.
Place the box in the same orientation it would be stored or stacked during its planned life (i.e., flat, not tilted). This way ensures that the box duplicates the conditions it would experience during actual use.
Step 4: Commencing the Examination
An initial step would involve activating the test once the box has been established in a correct location. Subsequently, the machine applies a gradually increasing compressive force to the box so that the test continues up to the point of collapse or excessive deformation of the box or until the box reaches a maximum predetermined force.
While carrying out the test, the machine will measure:
-
Force applied in each stage
-
Deflection (amount of deformation of the box)
-
Failure point (when the box fails to hold itself)
From the test results, it can be determined by box strength and how much pressure it can withstand.
Step 5: Observing and Recording Results
Observe the readings on the machine display during the process. Most updated box compression testers automatically record data and prepare reports for the following:
-
Maximum compressive force before failure
-
Deflection or deformation point
-
Compression strength
If graphical reports are available, they can be instrumental in providing a visualization to facilitate the interpretation of the obtained results.
Step 6: Interpretation of Results
With the completion of the test, analysis of the Box Compression Strength (BCS) necessitates consideration. BCS reflects the maximum load withstood by the box before failure; the higher the BCS, the more robust the box can be said to be.
An early collapse of the box may suggest that one or more of the following attributes are weak:
-
Weak materials
-
Construction flaws
-
Insufficiently bonded layers
From here on, you can consider taking further steps in redesign and material selections to improve the performance capacity of the box.
Step 7: Repeat The Test
One of the points pertaining to reliability is that you will have to carry out tests on more than one sample. Usually, from 3 to 5 samples of any box type are tested to show consistency and account for variations in the manufacturing method, thus proving whether your packaging will satisfy the relevant standard.
Tips for Accurate Results:
-
Control Environmental Conditions: Perform the test in a room where environmental conditions are maintained. The performance of cardboard is affected by temperature and humidity. Therefore, to get precise results, ensure that environmental conditions match with the environment in which the box is to be used.
-
Machine Calibration at Intervals: Periodic calibration of the equipment is important to have accuracy. Over time, very small misalignments or wear and tear affect accuracy.
-
Sample Consistency: All the test samples should be from the same production batch to minimize the variation.
Conclusion
The Box Compression Test Machine is a basic tool utilized to test packaging durability. In principle, it assures that your boxes can withstand all the risks and stress risks during transportation or storage. This can be accomplished by following the right setup and test procedures, which can, in part, get accurate data to optimize your designs for packaging and minimize damages that occur in the product, along with increasing satisfaction from the customers.
Understanding the effective use of this type of equipment avoids expensive mistakes, enhances product protection, and fulfills industry demands. In terms of testing new packaging systems as well as doing analysis of existing materials, box compression testing can offer the best understanding regarding how strong and reliable your packaging solutions are.
By having BCT testing done regularly within the quality control processes, you could ensure that your boxes are going to be cost-effective yet strong enough to keep your products safe throughout all aspects of shipping and handling.

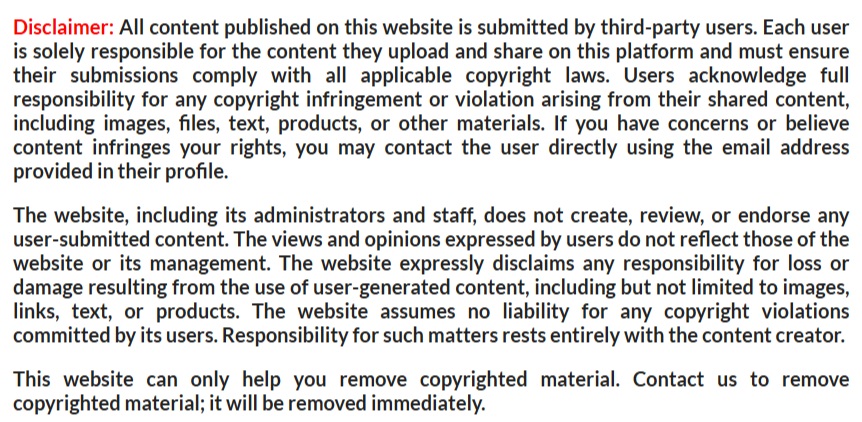
Comments
0 comment