views
Nickel 201 Screw
When it comes to choosing the right material for screws in industries that demand high performance, Nickel 201 stands out as a top choice due to its exceptional corrosion resistance, strength, and versatility. Nickel 201 is a high-purity, low-carbon version of nickel that offers remarkable properties for a wide range of applications. In this blog, we will explore the uses and benefits of Nickel 201 screws across various industries, and why they are an essential component in many critical applications.
What is Nickel 201?
Nickel 201 is a commercially pure nickel alloy with a composition of at least 99.6% nickel. It is known for its excellent corrosion resistance, particularly in reducing environments, and high electrical and thermal conductivity. Nickel 201 is often used in industries where high strength, resistance to corrosion, and the ability to maintain integrity at elevated temperatures are critical.
Key Features of Nickel 201 Screws
Before diving into the applications, it's important to understand the core features of Nickel 201 screws:
-
Corrosion Resistance: Nickel 201 is highly resistant to corrosion in a wide range of corrosive environments, including organic acids and caustic alkalis. It performs exceptionally well in environments that involve acids like hydrochloric, sulfuric, or phosphoric acid.
-
High Temperature Resistance: Nickel 201 screws maintain their mechanical properties in temperatures up to 600°F (315°C), making them ideal for applications that require resistance to thermal stress.
-
Electrical and Thermal Conductivity: Nickel 201 offers high electrical conductivity, which is important in applications involving electrical components or systems. It also has excellent thermal conductivity, making it a popular choice for heat exchangers and thermal systems.
-
Machinability: Nickel 201 is relatively easy to machine, which is essential for creating precise screw designs, threads, and fittings. This makes it suitable for custom-made screws in specialized applications.
-
Strength and Durability: While it’s not as strong as some other alloys, its strength-to-weight ratio, combined with its ability to resist oxidation and wear, makes it a reliable material for screws in industrial uses.
Common Applications of Nickel 201 Screws
Now, let's delve into the specific industries and applications where Nickel 201 screws are used.
1. Chemical Processing Industry
Nickel 201 screws are commonly used in the chemical processing industry, particularly in equipment that handles corrosive materials. Because of its excellent resistance to acids, caustics, and alkaline environments, Nickel 201 is the material of choice for screws used in reactors, tanks, pipes, valves, and other fittings that come into contact with harsh chemicals.
In applications where corrosive liquids like hydrochloric acid, sulfuric acid, or even seawater are involved, using screws made from Nickel 201 ensures the structural integrity of equipment over time. Its resistance to pitting and crevice corrosion adds an extra layer of reliability in these critical settings.
2. Aerospace and Aviation
The aerospace industry demands materials that can withstand extreme conditions such as high pressure, temperature, and harsh environments. Nickel 201 screws are commonly used in various parts of aircraft, engines, and components exposed to these conditions.
For example, Nickel 201 screws are used in turbine engines, fuel tanks, and exhaust systems, where heat resistance and the ability to perform in corrosive environments are key. Nickel's resistance to oxidation and thermal expansion makes it a preferred choice for critical aerospace applications.
3. Marine and Offshore Applications
Due to its excellent resistance to saltwater corrosion, Nickel 201 is often used in marine and offshore oil drilling applications. Marine equipment like ship hulls, underwater pipelines, and offshore platforms must withstand constant exposure to seawater, which is highly corrosive.
Nickel 201 screws and fasteners are essential in ensuring the durability of equipment used in these environments, preventing premature degradation caused by rust and corrosion. From screws in marine engines to those used in underwater construction, Nickel 201 provides long-lasting performance in saltwater conditions.
4. Electronics and Electrical Equipment
Nickel 201 is widely used in electronics and electrical applications where high conductivity is necessary. As a material with excellent electrical properties, it is ideal for screws used in electric motors, connectors, and components requiring high electrical conductivity.
Screws made from Nickel 201 can be found in transformers, capacitors, and other equipment where low electrical resistance is a key factor. Its reliability in providing a stable connection makes it a popular choice for manufacturers of electronic devices.
5. Food Processing Industry
The food processing industry demands the highest standards of cleanliness and durability for all equipment involved in food production. Nickel 201 screws are non-reactive with food products, making them an ideal choice for food processing machinery.
These screws are used in the production lines of various food products, including those that deal with acidic or salty substances. Their corrosion resistance ensures that they won’t affect the quality of the food products or contaminate them with unwanted materials.
6. Petrochemical Industry
The petrochemical industry, which deals with crude oil, natural gas, and the production of various chemicals, requires materials that can withstand high pressures, temperatures, and corrosive environments. Nickel 201 screws are often used in the construction and maintenance of pipelines, refineries, and pressure vessels.
These screws are essential in ensuring the structural integrity of equipment involved in drilling and processing, as they can withstand both the corrosive nature of the fluids and the elevated temperatures typical of petrochemical operations.
Advantages of Using Nickel 201 Screws
-
Longer Lifespan: Due to its exceptional resistance to corrosion, Nickel 201 screws last longer, reducing the need for frequent replacements and lowering maintenance costs.
-
Versatility: Nickel 201 can be used in a broad range of industries, from chemical processing to aerospace, making it a highly versatile material.
-
High Performance in Harsh Conditions: Nickel 201’s ability to withstand extreme temperatures, corrosive environments, and mechanical stress makes it a reliable choice for demanding applications.
-
Compliance with Industry Standards: Nickel 201 screws meet various international industry standards for corrosion resistance, ensuring they are up to the task for many critical applications.
Conclusion
Nickel 201 screws are an excellent choice for a wide range of industries that require materials capable of withstanding extreme environments. Whether in aerospace, marine, food processing, or chemical industries, the durability, corrosion resistance, and high-temperature performance of Nickel 201 screws make them indispensable for the longevity and reliability of critical systems and machinery.
Choosing Nickel 201 screws ensures that equipment remains durable, efficient, and free from corrosion, ultimately enhancing the safety and performance of various industrial processes. So, when you're looking for screws that can stand up to the harshest conditions, Nickel 201 is a choice that offers reliability and longevity.
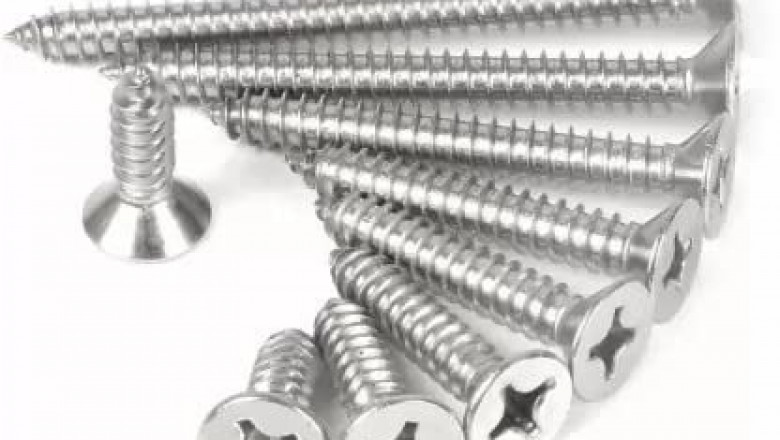

Comments
0 comment