views
Conventional Material Handling Methods
Forklifts remain a mainstay for material movement in warehouses and manufacturing facilities. Forklifts come in various sizes and lifting capacities depending on the loads they are handling. Gasoline or diesel powered internal combustion engines provide the necessary power and lifting capabilities for loads weighing several thousand pounds. Pallet jacks and hand trucks are mainstays as well for transferring loads that individuals can manually move. Pallet jacks roll under a pallet and are used to transport loads on pallets or skids to different areas or shelves. Hand trucks are used in a similar manner but are often designed for smaller, more delicate loads that cannot tolerate being set directly on the ground.
Conveyor Systems Speed Material Flow
Conveyors make up an integral part of modern Material Handling Equipment, shuttling boxes, packages, pallets and other loads between different areas and workstations. Belt conveyors consist of a continuous loop of metal or plastic belt with rollers which product rides on. Belt speeds can range from just a few feet per minute up to hundreds of feet per minute depending on the distance traveled and operating environment. Roller conveyors utilize a series of rotating cylinders rather than a continuous belt to smoothly transport loads. Spiral conveyors are useful for inclining product up or down between different elevations. Pallet conveyors are sturdier belt or roller types designed specifically for full pallets of product. Automated guided vehicles also augment conveyor systems, navigating factory floors to transport materials between machines or storage areas.
Automated Storage and Retrieval Systems Grow in Popularity
Automated storage and retrieval systems (AS/RS) are an increasingly utilized alternative to traditional rack style warehousing. With AS/RS, storage racks are stationed vertically and loads are shuttled to and retrieved from the racks by load handling machines capable of precise vertical and horizontal movements. This multi-level storage maximizes space utilization while load handling equipment eliminates the need for workers to manually access different rack levels. Carousels provide continuous rotation of product for easy pickups. Mini-load AS/RS are designed for individual cases or boxes while unit-load models can accommodate full pallets. Robotic mobility is also being introduced which allows autonomous vehicles to retrieve and deliver loads within AS/RS.
Robotic Material Handling Revolutionizes Manufacturing
Robotics have transformed material handling within factory environments. Articulated robots seamlessly integrate with production machinery for on-the-fly part transfers. Robotic arms precisely place components into position for assembly or packaging. Multi-axis robots optimize component loading patterns to streamline work-in-progress inventory flows between workcenters. Mobile robots autonomously transport materials within facilities or even between buildings on a campus. Collaborative robots work safely alongside humans for applications involving heavy components or repetitive movements. Exoskeletons augment worker strength and endurance for material handling tasks. Machine vision, sensors and advanced controls allow robots to effortlessly "see" components and cooperate with machines and people on a plant floor. Overall, robotics boost throughput, quality and workplace safety within material flows.
Emerging Technologies Push Envelope for Material Handling
New technologies on the horizon promise to further revolutionize logistics and manufacturing material flows. Exoskeletons, autonomous guided vehicles, cobots and smart robotics are rapidly commercializing to augment human labor and streamline materials management. Additive manufacturing or 3D printing brings component manufacturing directly to the point of use. Drones and driverless vehicles will transport goods between warehouses and factories. Internet of Things connectivity, cloud computing, machine learning and other Industry 4.0 concepts optimize material flows through real-time instrumentation, predictive analytics and adaptive controls. Technologies like augmented and virtual reality will train employees and interface with material handling equipment in new ways. Overall, emerging technologies will transform what's possible for automating logistics systems and productive factory material flows in the coming years.
material handling encompasses the methods, equipment and systems for transporting, storing and protecting physical goods throughout supply chains and production networks. Conveyors, forklifts, automated guided vehicles and robotics currently power sophisticated materials flows. Automated storage and retrieval systems optimize warehouse space utilization. Going forward, emerging technologies including Artificial Intelligence, exoskeletons, autonomous vehicles and additive manufacturing will push the boundaries of next-generation material handling solutions and fundamentally change manufacturing operations. Continuous innovation will be needed to match the increasing speed, precision and customization demands placed on modern integrated logistics networks.
Get this Report in Japanese Language:
Get this Report in Korean Language:
About Author:
Money Singh is a seasoned content writer with over four years of experience in the market research sector. Her expertise spans various industries, including food and beverages, biotechnology, chemical and materials, defense and aerospace, consumer goods, etc. (https://www.linkedin.com/in/money-singh-590844163)
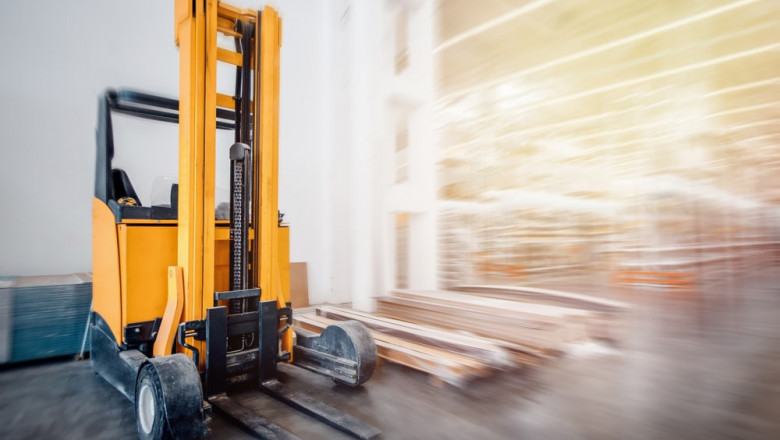

Comments
0 comment