views
https://ebeammachine.com/a-guide-to-the-electron-beam-machining-process/
In the ever-evolving world of manufacturing, technological advancements play a pivotal role in enhancing precision, efficiency, and capabilities. One such breakthrough that has gained immense traction in recent years is Electron Beam Machining (EBM). This highly specialized technique, often seen as a game-changer, is revolutionizing material processing across various industries, including aerospace, medical, automotive, and electronics. Let’s explore how electron beam machining is transforming material processing and why it’s considered a futuristic approach.
What is Electron Beam Machining?
Electron Beam Machining is a non-contact, thermal process that utilizes a focused stream of high-energy electrons to machine materials. The process involves firing an electron beam at the workpiece, where the electrons impart kinetic energy to the atoms in the material, causing localized melting or vaporization. The focused electron beam has an extremely high intensity, enabling it to perform intricate and precise operations on a wide range of materials, from metals and alloys to ceramics and composites.
EBM is performed in a vacuum chamber, which ensures that the electron beam travels without interference from air particles, maintaining its focused intensity. This vacuum environment also eliminates oxidation and contamination during the machining process, making it ideal for high-precision operations.
Precision and Accuracy Like Never Before
One of the most significant advantages of electron beam machining is its unparalleled precision and accuracy. Unlike traditional machining methods that rely on physical tools like drills, cutters, or abrasives, EBM uses the energy of electrons to remove material, offering incredible control over the process. The fine focus of the electron beam allows for the creation of very small, intricate features, such as holes, slots, and grooves, with micron-level precision.
This extreme accuracy is especially beneficial in industries where minute tolerances are essential. For example, in the aerospace industry, where parts such as turbine blades or aircraft components require incredibly tight tolerances, EBM ensures that the material is machined to exact specifications without the risk of warping or distortion.
Material Versatility
Electron beam machining is capable of working with a broad range of materials that are difficult to machine using traditional methods. Hard-to-cut materials like titanium, superalloys, stainless steel, and high-melting-point metals, as well as advanced ceramics and composites, are easily processed with EBM. These materials, which would typically present challenges with conventional cutting tools, can now be machined with exceptional precision and efficiency using the electron beam.
Moreover, EBM is particularly effective for materials that are prone to heat distortion when subjected to conventional machining techniques. Since the electron beam’s energy is concentrated in a very small area, the surrounding material experiences minimal heat buildup, reducing the chances of thermal distortion. This makes EBM an ideal choice for precision parts in industries that demand high-performance materials, like aerospace, medical implants, and semiconductor manufacturing.
Minimal Tool Wear and Maintenance
Another striking advantage of electron beam machining is that it eliminates the need for physical cutting tools. In conventional machining methods, tools are subjected to wear and tear, leading to frequent maintenance, replacement costs, and extended downtime. EBM, on the other hand, uses an electron beam, which doesn’t suffer from wear and tear in the same way. This means less downtime, fewer tool replacements, and a significant reduction in overall maintenance costs. This also results in consistent performance over time, ensuring the precision of the final product remains unaffected throughout the machining process.
Complex Geometries Made Possible
Electron beam machining is especially suited for creating complex shapes and intricate geometries. The focused electron beam can be directed with such precision that it can cut, drill, or weld even the most challenging contours and complex 3D structures. This capability is invaluable in industries like aerospace, where components often feature sophisticated geometries that cannot be achieved using traditional machining tools.
In addition to cutting, EBM can also be used for welding and surface treatment, allowing manufacturers to join materials with extreme precision. This flexibility makes EBM an attractive option for prototyping, small batch production, and high-precision custom components that would be impossible to achieve through conventional methods.
High-Speed and Efficiency
While electron beam machining is known for its precision, it also offers speed and efficiency. The electron beam can remove material quickly and precisely, without the need for physical tools or excessive force. This results in faster production times and increased throughput. Moreover, since the process takes place in a vacuum, there is no need for coolant or lubricant, which streamlines the entire process, reducing operational costs.
The high-speed nature of EBM makes it an ideal choice for industries requiring rapid prototyping or the production of small to medium-sized batches. Unlike conventional machining methods, which may require lengthy setup times and tool changes, electron beam machining can maintain a consistent level of performance throughout the production cycle.
Sustainability and Clean Processing
In an age where sustainability is a priority, electron beam machining stands out as an eco-friendly solution. Since the process doesn’t rely on cutting tools or generate significant amounts of waste, it produces minimal material scrap. Additionally, the absence of coolant or lubricant reduces the environmental impact and minimizes the risk of contamination. The vacuum environment also prevents oxidation, ensuring that the machined parts retain their high-quality finish without the need for additional post-processing.
For industries focused on sustainability, such as the renewable energy sector, the green benefits of EBM are particularly attractive. Its low waste and energy-efficient process make it a step toward more environmentally conscious manufacturing practices.
Applications Across Industries
The impact of electron beam machining is most evident across several industries. Some key applications include:
1. Aerospace Industry: EBM is used to produce intricate, high-performance components like turbine blades, engine parts, and aircraft structures that require extreme precision.
2. Medical Sector: In the medical field, EBM is used to manufacture complex implants, surgical tools, and devices that demand biocompatibility and precision.
3. Electronics: EBM plays a vital role in the production of semiconductors and microelectronics, where precision and minimal thermal impact are essential.
4. Automotive: The automotive industry uses EBM to create high-strength, lightweight parts for performance vehicles and specialized components.
5. Energy Sector: In energy, particularly in nuclear and renewable energy applications, EBM is used to fabricate components that can withstand extreme conditions.
Conclusion
Electron beam machining is undoubtedly revolutionizing material processing, offering significant advancements in precision, efficiency, and versatility. Its ability to work with hard-to-machine materials, create complex geometries, and eliminate tool wear while maintaining exceptional speed has made it an indispensable technology across a range of industries. As industries continue to push the boundaries of innovation and complexity, the role of electron beam machining will only grow, driving more sustainable, precise, and efficient manufacturing practices worldwide.
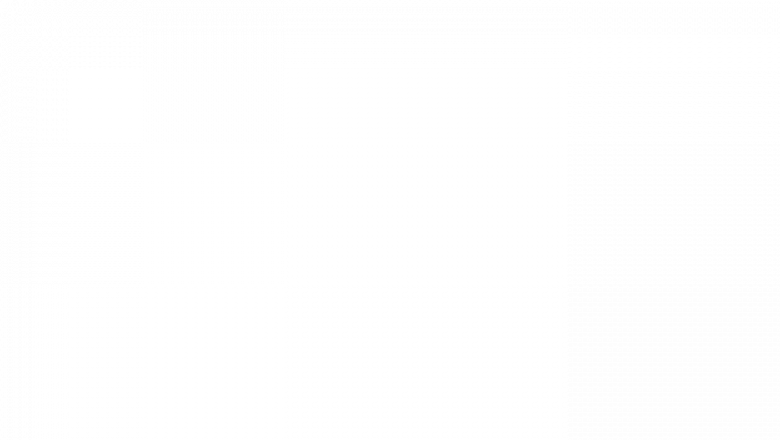

Comments
0 comment