views
Introduction
We’re living in a world where machines talk to each other, data flows nonstop, and downtime is just… not an option. Welcome to Industry 4.0—the fourth industrial revolution—where smart factories are the new norm, and predictive maintenance is becoming the secret sauce behind unstoppable efficiency.
Think about it: What if your machines could tell you they’re about to break before they actually do? That’s the power of predictive maintenance (PdM) market—and it’s flipping the traditional maintenance game on its head.
Understanding Predictive Maintenance
Predictive maintenance isn’t just a fancy term—it’s a game-changing approach to equipment upkeep.
At its core, predictive maintenance uses data and technology to predict when equipment will fail. This way, businesses can schedule repairs before the breakdown happens.
The global Predictive Maintenance Market size was valued at USD 5.93 billion in 2023, and is predicted to reach USD 32.30 billion by 2030, at a CAGR of 27.4% from 2024 to 2030.
How is it different from other types of maintenance?
· Reactive Maintenance: Fix it when it breaks.
· Preventive Maintenance: Fix it on a schedule, whether it needs fixing or not.
· Predictive Maintenance: Fix it only when data shows it’s about to fail.
Technologies Powering Predictive Maintenance
PdM wouldn’t exist without a few cutting-edge tech heroes working behind the scenes.
Internet of Things (IoT)
Sensors embedded in machines continuously gather data—temperature, vibrations, noise, and more. IoT acts as the nervous system of predictive maintenance.
Artificial Intelligence (AI) and Machine Learning
AI analyzes that sensor data and finds patterns that humans might miss. Machine learning models learn over time, making predictions more accurate.
Big Data Analytics
Massive volumes of data are no good unless you can analyze them. Big data tools help turn raw numbers into actionable insights.
Cloud Computing
Data storage and processing happens in the cloud, allowing easy access and collaboration across teams and locations.
Benefits of Predictive Maintenance in Industry 4.0
Why are companies jumping on the PdM train? Because the benefits are huge.
Reduced Downtime
Unplanned breakdowns? Say goodbye. Predictive maintenance keeps your machines running longer and smoother.
Cost Efficiency
No more unnecessary routine checks. You only fix what needs fixing, saving big on labor and parts.
Enhanced Equipment Lifespan
Treat your machines right, and they’ll return the favor. PdM helps equipment last longer with fewer surprises.
Improved Safety and Compliance
By catching issues early, you reduce risks to employees and avoid failing inspections or breaking regulations.
Use Cases Across Industries
Predictive maintenance isn’t just for one type of business—it’s revolutionizing a ton of industries.
Manufacturing
Assembly lines can’t afford hiccups. PdM keeps production rolling and defect rates down.
Oil and Gas
Remote rigs rely on equipment health. PdM alerts operators about potential leaks or wear before disaster strikes.
Transportation and Logistics
Trucks, planes, and trains need to stay on schedule. PdM ensures fleets are in top shape and reduces repair costs.
Energy and Utilities
Grid systems, turbines, and generators benefit from early fault detection—minimizing outages and maximizing output.
How Predictive Maintenance Works
Let’s break down the step-by-step process.
Data Collection
Sensors installed on equipment gather data 24/7. Think of it like your machine’s fitness tracker.
Condition Monitoring
This data is monitored in real time. If something’s off—say, a spike in vibration—it gets flagged.
Predictive Algorithms
Machine learning steps in, analyzing the data against failure models to predict when something might go wrong.
Maintenance Scheduling
Once a potential issue is identified, a work order is automatically created—before a breakdown happens.
Challenges in Adopting Predictive Maintenance
PdM isn’t all sunshine and savings—it comes with a few bumps in the road.
Data Security and Privacy
More data means more risk. Companies need to protect sensitive machine data from cyber threats.
High Initial Investment
Sensors, platforms, and training require upfront costs. But long-term savings usually outweigh the setup expenses.
Skills Gap
Many companies struggle to find workers who understand both industrial machinery and data science. Bridging this gap is critical.
Best Practices for Implementation
Want to make PdM work for your business? Follow these tips:
Start Small and Scale
Begin with a pilot program on one piece of equipment. Measure results, then expand.
Choose the Right Tools
Not all PdM platforms are created equal. Find one that fits your industry and goals.
Employee Training
Don’t forget your team! Make sure they’re trained on how to use the tools and respond to alerts.
Continuous Monitoring and Evaluation
PdM is not set-it-and-forget-it. Keep refining your models and processes to boost accuracy.
The Future of Predictive Maintenance in Industry 4.0
The PdM journey is just getting started. Here’s what’s next:
Integration with Digital Twins
Digital replicas of equipment let you test changes virtually before applying them in the real world.
Autonomous Maintenance Systems
AI-powered robots that diagnose and fix problems without human help? It’s closer than you think.
Edge Computing and Real-Time Analytics
Processing data right at the source (instead of the cloud) means even faster response times.
Conclusion
Predictive maintenance isn’t just a trend—it’s a full-on revolution in how we manage industrial equipment. By shifting from guesswork to data-driven action, businesses are saving money, boosting safety, and staying ahead of the competition.
In the age of Industry 4.0, staying reactive just won’t cut it anymore. Predictive maintenance is the future—and the future is now.
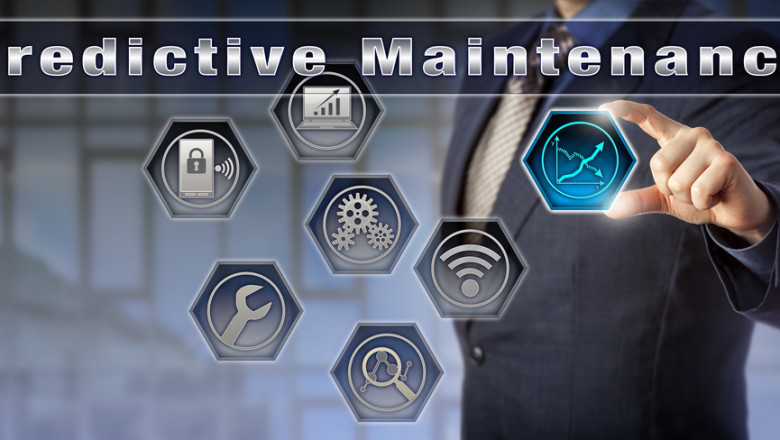
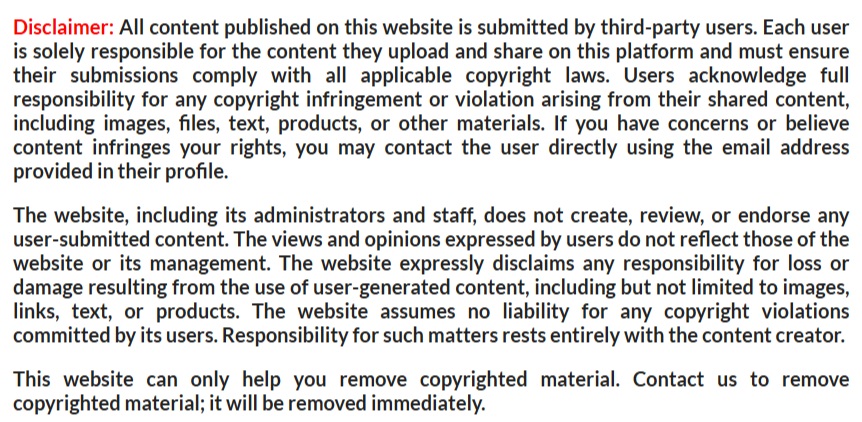
Comments
0 comment